DTF Film Selection & Variations: Choosing the Right Glossy, Matte, Hot Peel, or Cold Peel for Your Printing Needs
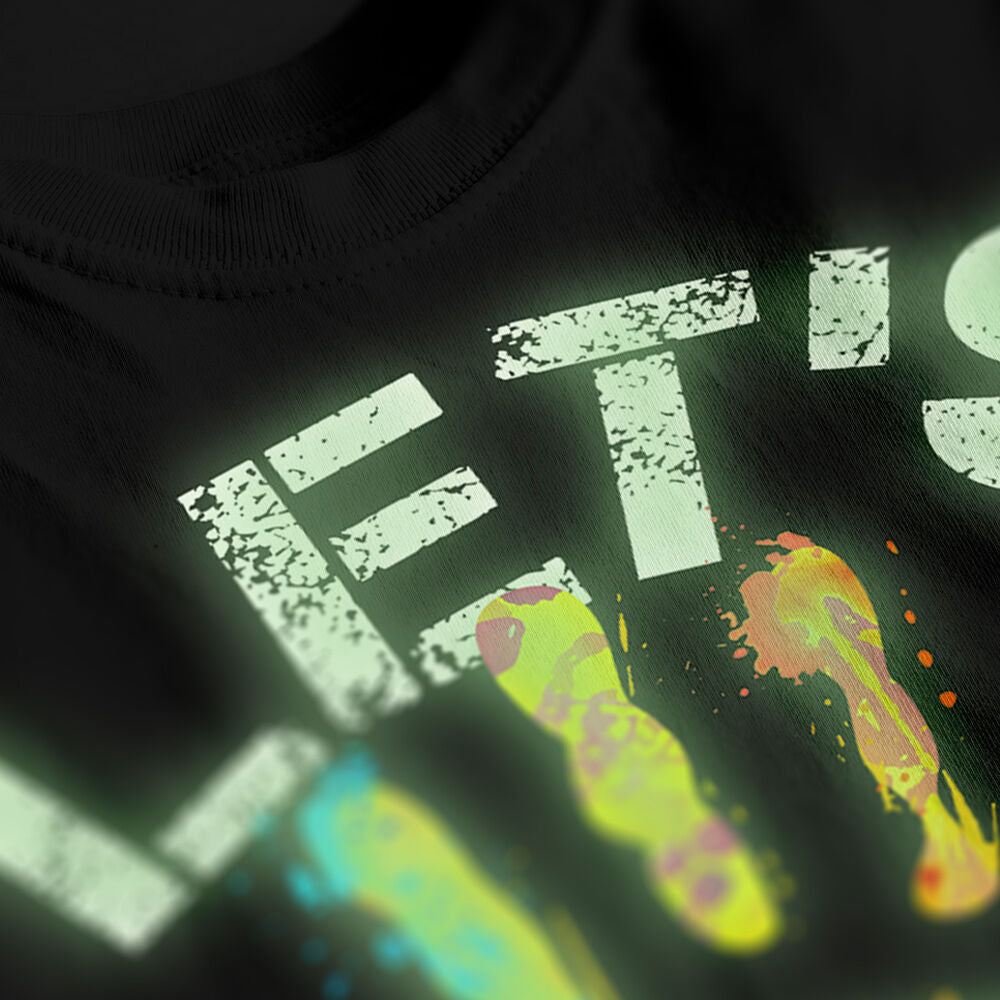
What Is This Article About?
Curious about which DTF film delivers the best results for your business? In this comprehensive guide, we break down the differences between glossy, matte, hot peel, and cold peel films, explaining how each choice affects color vibrancy, durability, and overall print quality. Discover expert insights to help you pick the perfect film for any fabric or design requirement.
Direct-to-Film (DTF) printing relies on a special PET transfer film as the carrier for ink. Choosing the right film type is crucial, as it impacts everything from color vibrancy and ink adhesion to ease of use and durability. For RIP software that optimizes film performance, check Caldera or Onyx Graphics. For beginners just starting out, check our introduction to DTF printing first. The FESPA recommends understanding film selection as a critical factor in print quality. This section explores the various DTF film options—glossy vs. matte finishes, cold peel vs. hot peel release methods, and films specialized for different fabrics—and explains how each variation performs in terms of ink adhesion, color output, durability, and fabric compatibility.
Glossy vs. Matte DTF Films
DTF transfer films come with different surface finishes, typically categorized as glossy or matte. This finish refers to the texture of the film's coated side (the side that receives the ink). The finish affects the look of the printed transfer and can influence how the ink behaves. When selecting DTF consumables, understanding film types is essential. Also see our guide on adhesive powder application for complete transfer success:
-
Glossy Films: Glossy DTF films have a smooth, reflective coating that yields a shiny print. They tend to enhance the vibrancy and depth of colors, making prints appear more saturated and eye-catching. The glossy surface reflects light, giving the final transfer a sheen. Because of their high ink receptivity on a smooth coating, glossy films can produce very bright images with sharp details. This makes them popular for designs that need to "pop" with vivid color (for example, prints on dark polyester where you want maximum brightness). Leading manufacturers like Roland DG and Epson Professional Imaging recommend glossy films for vibrant designs. For optimal results with glossy films, proper color management and ICC profiles are crucial, as outlined by the International Color Consortium. However, the high sheen can sometimes highlight any imperfections and can create glare in certain lighting. In terms of ink adhesion, quality glossy films are formulated to hold ink well, but lower-quality ones might allow slight smudging if the ink doesn't anchor firmly. Some printers also note that glossy films can be a bit trickier to handle. Equipment from Mimaki includes anti-static features —the unprinted side is slick, which can cause static or slippage in some printers' feed mechanisms. Manufacturers often mitigate this by making the non-print side distinctly smooth and clear, so operators can easily identify the printable side.
-
Matte Films: Matte DTF films have a dull, frosted or non-reflective coating. They produce a softer-looking print with minimal glare. Colors on matte films are slightly more subdued or "natural" in appearance compared to glossy. Rather than a shiny finish, matte transfers have a flat look that can be desirable for a more subtle or premium aesthetic. When preparing artwork for DTF printing, consider how different finishes will affect the final appearance. For color accuracy, explore our advanced color management guide. Matte coatings typically allow the ink to absorb a bit more into the layer, which can help preserve fine details and line work. In fact, high-grade matte films often have an evenly distributed coating that absorbs ink uniformly, enabling crisp detail and high ink loads without bleeding. This can result in excellent ink adhesion—ink bonds tightly into the matte receptive layer. The hand feel of a matte film transfer on fabric is often described as soft or smooth, since the print doesn't have a plasticky shine. In terms of longevity, matte films are often praised for producing transfers that resist fading or peeling over many wash cycles. Because the ink and adhesive bond well in the textured coating, the prints tend to stay intact. Ease of use is also a factor: many matte DTF films are double-sided matte, meaning both sides have a coating. The back side's coating adds a bit of friction and anti-static property, which can improve printer handling. This design prevents sheets from sticking together and keeps the film feeding straight. As one source notes, a double-matte film is more stable in printers (less slipping) and effectively reduces static issues during printing. These features are helpful in high-volume environments.
When to use Glossy vs. Matte: The choice between glossy and matte film often comes down to the desired appearance and the garment/fabric color. According to Impressions Magazine, glossy films are excellent for vibrant, eye-catching designs – for instance, a full-color logo on a polyester jersey might benefit from the color "pop" a glossy film provides. Matte films are preferred for a soft look or vintage style designs – for example, a distressed graphic on a cotton shirt where a muted finish suits the theme. When working with specialty inks and finishes, film choice becomes even more critical. Check our troubleshooting guide if you encounter film-related issues. Matte films can also be advantageous when printing on light-colored or natural fabrics like cotton, where a glossy sheen might look out of place. From a durability standpoint, many printers lean toward matte films if maximum wash endurance is a priority, as the matte-coated transfers are noted to hold up with less risk of cracking or peeling over time. On the other hand, if color vibrancy is the top requirement and you don't mind a bit of shine, a glossy film can deliver extremely rich color saturation. It's worth noting that the final finish of the garment can also be adjusted using finishing sheets (for example, pressing with a matte finishing sheet to dull a glossy print), but fundamentally the film's inherent finish sets the baseline look. In summary, glossy DTF film provides a shiny, high-contrast look that makes colors stand out, whereas matte DTF film offers a smooth, glare-free look with potentially longer-lasting color stability.
Cold Peel vs. Hot Peel Films
Beyond the surface finish, DTF films are distinguished by their peel method: cold peel vs. hot peel. This refers to the temperature at which you remove (peel off) the PET film after heat-pressing the transfer onto the fabric. Understanding the proper heat press settings for each type is essential. Regular printer maintenance also ensures optimal film performance. The two types use different release coatings that behave uniquely, affecting workflow, appearance, and durability.
-
Cold Peel DTF Film: Cold peel films must be allowed to cool down completely (or at least to a lukewarm state) before you peel the film off the garment. In practice, after you heat press the printed film onto the fabric with adhesive, you'll typically wait around 20–30 seconds (sometimes more for large prints or thicker films) until the transfer is cool to the touch, then peel away the PET carrier. The chemistry behind this is that cold peel films use a more robust adhesive/release layer (often an oil-based or silicone-based coating) that sets as it cools. Proper adhesive powder application is crucial for cold peel success. Consider exploring specialty finishes that work best with cold peel films. This type of coating bonds the ink and adhesive firmly to the fabric once fully cooled, resulting in very durable transfers. One advantage of cold peel is excellent ink adhesion and detail – the film holds onto the ink during printing and pressing, releasing only once solidified, which means even fine details and small text come out clean without partial lifting. Cold peel transfers often have a matte or semi-matte finish on the shirt (many cold-peel films themselves have matte coatings). In terms of color, cold peel prints may appear slightly less glossy compared to hot peel; some describe the colors as having a "textured" or matte look. However, they are still very vibrant, and importantly, they tend to retain their color through washes exceptionally well. Because the adhesive bond is strong and flexible, cold peel transfers cope with repeated laundering with minimal fading or cracking. According to Specialty Graphic Imaging Association (SGIA) standards, endorsed by ASTM International, cold peel DTF film often outperforms hot peel in long-term wash durability, with less chance of the design peeling or colors dulling over time. Cold peel film is also more forgiving with different fabrics: it works effectively on a wide range of materials, including those that may be heat-sensitive or have textured surfaces. For example, on thick or rough fabrics (canvas, burlap, or even surfaces like tarpaulin), as tested by SGS Textiles, the cold peel process gives the material a moment to cool and stabilize, preventing wrinkles or damage that a hot peel might cause. The trade-off with cold peel is speed. Since you must wait for cooling, production is slower. In a busy shop, this means a longer cycle per garment – you can't immediately remove the carrier and move to the next garment. For high-volume operations, consider scaling your DTF production workflow. If you try to peel too soon, you risk distorting or ruining the print (the ink layer might not have set and could lift off). Thus, cold peel is often recommended for quality-focused or detailed work and for scenarios where longevity is paramount (e.g. high-end custom apparel or items expected to endure many washes).
-
Hot Peel DTF Film: Hot peel films are designed to be peeled off immediately (or within just a few seconds) after the heat press, while the print is still hot. The release layer in hot peel film usually contains a special wax-based or water-based coating that doesn't require cooling to release; in fact, it must be peeled hot before it fully resolidifies. This allows for a fast workflow: as soon as the heat press opens, you can peel the film off in one smooth motion and the transfer is complete. For high-volume production, this is a huge benefit. To learn the complete process, see our guide on how to apply DTF transfers. A shop using hot peel films can press and peel one transfer after another without pause, potentially pressing dozens more shirts per hour than a cold peel process would allow. For example, a manufacturer noted that using hot peel film made it feasible to output nearly 100 transferred shirts in an hour, since there's virtually no wait time between presses. In terms of color and appearance, hot peel transfers often look glossier and very vibrant right after peeling. The immediate peel can impart a slightly shiny finish on the print (some printers describe the colors as "brighter" with hot peel). This can be great for bold designs on sports uniforms or merch where turnaround and impact are key. However, there are some drawbacks to hot peel films. Because the release layer is formulated to let go quickly, it can sometimes mean the ink layer doesn't have quite as strong a bond to the fabric as a cold peel would achieve. Many users observe that hot peel transfers, while initially strong, may not have the same wash longevity – over multiple laundry cycles, there might be a bit more cracking or fading compared to cold peel transfers. The adhesive used in hot peel films can be a tad less robust in the long term (one reason being many hot-peel coatings are water-based, which can have lower water-wash fastness ). If you encounter issues, consult our DTF troubleshooting guide. For advanced techniques, see our color management strategies. In fact, if a hot-peeled transfer isn't done perfectly, the design can even peel off in places during the peel if the glue re-hardened (which is why manufacturers stress peeling while it's still hot). Another consideration is fabric compatibility: while hot peel films can be used on most of the same fabrics, the quick removal can sometimes cause issues on certain materials. For instance, very stretchy or delicate fabrics (thin nylon, some polyesters, or anything that might shrink or warp from heat) could get slightly distorted if the film is yanked off too quickly while the garment is hot. Cold peel gives those fabrics time to cool flat. With hot peel, you have to ensure proper temperature and pressure; these films often press at a bit lower temperature (around 140–150°C) for a short time, which helps prevent damage and allows quick release, but you also must be precise—there's less margin for error in pressing parameters with hot peel films. In summary, hot peel DTF film is ideal for speed and efficiency, enabling rapid production with bright results, while cold peel film is chosen for maximum durability, detail, and versatility with different fabrics.
Choosing Cold vs. Hot Peel: The "better" film depends on your application. If you run a production line for team jerseys or event merchandise where dozens or hundreds of prints are needed quickly, as documented by Printwear Magazine, hot peel film can dramatically improve throughput. For businesses exploring different DTF business models, understanding film types is crucial. The slight sacrifice in ultimate wash durability might be acceptable if the items are short-term (e.g. event t-shirts or seasonal jerseys that won't be washed for years on end). On the other hand, if you are producing retail-quality apparel or items meant as keepsakes, cold peel is often recommended for its stronger, longer-lasting bond. Many professionals actually keep both types in stock and use hot peel for rush jobs or large solid designs, and cold peel for intricate or high-end jobs. It's also worth noting that the industry has introduced some "hybrid" or universal DTF films that claim to allow both hot or cold peeling. For example, certain premium films are marketed as hot/cold peel, meaning you can peel warm for convenience or let it cool for a more matte finish and durability. These films aim to combine flexibility and are useful if you want one film for all scenarios. Regardless of type, always follow the manufacturer's guidelines on press temperature and timing: hot peel films typically activate around 140–150°C for ~8–10 seconds. Equipment from Stahls' and Polyprint are calibrated for these specifications, whereas cold peel films often press at 150–160°C for ~10–20 seconds and need that cooling period. Following these specs will ensure the best ink adhesion and release. To summarize, use hot peel when fast application is crucial and the prints only need standard durability, and use cold peel when you need the sturdiest, most wash-resistant transfers or when printing on tricky fabrics that benefit from a cooling phase.
Specialized Films for Different Fabrics
One of the advantages of DTF technology is that it can adhere to a wide variety of fabrics – cotton, polyester, blends, and even traditionally hard-to-print materials like nylon or silk. For a comprehensive comparison with other methods, see our guide on DTF vs screen printing, sublimation, DTG, and vinyl. However, no single film is perfect for every fabric, and manufacturers have developed specialized films or tweaks to get the best results on different material types. When selecting a film, consider the fabric composition of the target garment and any special requirements (stretchiness, heat sensitivity, etc.):
-
General-Purpose vs. Fabric-Specific Films: Most standard DTF films are designed to be fairly universal, with leading suppliers like Chemica and Siser offering comprehensive solutions, working on the common apparel fabrics. For instance, a high-quality "universal" film will advertise strong adhesion on cotton, polyester, and poly-cotton blends alike. These films have coatings and adhesive properties balanced to provide good results on a broad range of fibers. An example is the Kodak KODACOLOR FTF (Film-to-Fabric) DTF film, which is marketed as being able to print on a wide variety of fabrics (natural cotton, polyester, nylon, rayon, blends, etc.) with durable results. Similarly, the Color Prime Universal DTF Film is described as delivering vibrant, long-lasting transfers on cotton, polyester, and blends without needing separate film types. These all-round films are excellent for shops that handle mixed orders – you can stock one film and confidently use it on a 100% cotton T-shirt one minute and a polyester athletic shirt the next. For proper equipment setup, check our complete DTF equipment guide. Ink adhesion and color vibrancy on these films are usually optimized for the "toughest" case (often polyester, since it's non-absorbent and can be challenging for transfers). For example, Color Prime's universal film has a high ink loading capacity and excellent ink absorption, ensuring sharp and vibrant prints on all supported fabrics. That said, even within universal films, you might choose a particular finish or peel type based on the fabric: e.g., using the matte version for cotton as it gives a soft feel, or a hot-peel version for quick poly jersey prints.
-
Cotton and Natural Fabrics: Cotton is a breathable, heat-tolerant natural fiber that generally works very well with DTF. It doesn't melt or warp under high heat, so you have flexibility in choosing film. For the best feel on cotton, many professionals prefer a matte, cold-peel film, which tends to produce a soft, seamless transfer that almost feels part of the fabric. A thin and flexible cold-peel film can move with the cotton's weave, minimizing any heavy "sticker" feel on the shirt. In terms of adhesion, cotton fibers are slightly porous and the molten adhesive from DTF can really grab onto them, so adhesion is usually strong. The main performance metric on cotton is color vibrancy – a good film will keep colors looking rich on cotton without the need for pretreatment (unlike DTG printing which needs pretreated cotton). For advanced color techniques, explore our guide on mastering DTF color accuracy. Films from major brands generally excel here; for example, prints made on a quality film remain bright on cotton and resist washing out, as long as the curing and pressing were done correctly. There isn't typically a need for a special "cotton-only" DTF film (as opposed to how in some other methods you have separate transfer paper for dark cotton vs light cotton, etc.), since the white ink in DTF covers dark cotton just fine. The key is choosing a film that gives the finish you want on cotton: matte if you want the design to blend more with the matte look of cotton fabric, or glossy if you want a decal-like shine. Example: A print shop might use a matte cold-peel film for printing a detailed graphic on a black cotton tee, to ensure the result has a soft hand and long-lasting image. The film's properties (good ink absorption and thin, flexible coating) will make the colors bright and the design durable on that cotton shirt.
-
Polyester and Synthetics: Polyester (and related synthetics like acrylic or poly blends) are also very popular in apparel, especially sportswear. DTF is well suited for polyester – unlike direct-to-garment methods, DTF doesn't require pretreat and the prints sit on the surface, which is ideal because poly doesn't absorb ink. However, polyester brings two challenges: heat sensitivity and dye migration. Polyester can scorch or melt if pressed too hot for too long, and certain poly fabrics (especially sublimated or rich-colored polyester) can bleed dye up into the transfer if the heat is high. Specialized DTF films (or more often, specialized adhesive powders) have been developed to address these issues. According to Printing Industries of America and TAPPI, proper temperature control is critical for synthetic fabrics. One approach is using lower-temperature DTF films: these are films formulated to transfer at a reduced temperature (for instance, ~120–130°C instead of the typical 150–160°C). By pressing at a lower temp, you minimize the polyester fabric's exposure to heat, reducing the risk of dye migration (where the garment's dye reactivates and discolors the transfer). In practice, you might extend the press time (even up to 40-50 seconds) at the lower temperature to ensure the adhesive fully melts and bonds. Not all standard films can cure properly at such low temperatures; thus, some films are marketed for "low temp application" specifically for polyester. If you work a lot with polyester jerseys or performance wear, it's wise to choose a film that explicitly states compatibility with poly. In terms of finish, glossy films are often used on polyester. Polyester's smooth surface combined with a glossy DTF film yields extremely vibrant, crisp prints – one FAQ notes that 100% polyester can yield sharper and more vibrant prints than cotton. The Color Prime film, for example, lists polyester as one of its primary compatible fabrics and achieves very bold color on it. Just be cautious with heat: many recommend using a slightly lower press temperature for polyester (if not using a special low-temp film, then at least at the lower end of the film's range, say 140°C) to avoid issues. Some DTF suppliers also offer an anti-migration powder or blocker underbase for polyester, but that veers into the adhesive realm rather than the film itself. Generally, a good film with a solid white ink underbase (often increased white ink percentage) will do the job for polyester. To summarize, choose a film that can handle lower heat and provides a strong bond for polyester. Many standard films do, but when in doubt, look for mentions of "polyester friendly" or consult the manufacturer's specs.
-
Stretchy Fabrics (Spandex, Lycra, Nylon): Fabrics like spandex, Lycra, and certain nylons (often used in athletic wear, swimsuits, leggings) are elastic and very smooth, which poses a unique challenge. The transfer needs to stretch with the fabric without cracking. For more on challenging materials, see our guide on DTF printing on difficult substrates. Here, the flexibility of the cured ink and adhesive layer is critical. Specialized DTF films for stretchable fabrics exist – they are formulated to yield a more elastic transfer. This might involve a slightly different chemistry that keeps the ink/powder layer pliable after curing. As one guide notes, when printing on very stretchy fabrics (nylon, spandex blends), it's important to use special DTF transfer films made to stretch and move with the fabric. These films, in combination with a stretch-compatible powder adhesive, allow the design to elongate with the garment and spring back without breaking. For example, an athletic compression shirt (poly-spandex mix) would benefit from a "stretch" DTF film that remains flexible; standard transfers might feel stiff and could crack when the material is fully stretched. Nylon is another tricky synthetic – pure nylon, like that found in windbreakers or flags, often has a waterproof coating or high surface tension that makes adhesion harder. Intertek Textiles provides comprehensive testing standards for these materials. Some DTF film suppliers recommend using a specific "nylon DTF" adhesive powder or even a pretreatment on nylon fabrics. The film itself should ideally be one that can handle strong bonding. A generic universal film may work on nylon, but results can vary; if you plan to decorate a lot of nylon (like team jackets), seek out any film that specifically mentions nylon compatibility (some do list nylon in their supported fabrics ). Additionally, hot vs. cold peel matters here: for stretchable and delicate fabrics, cold peel films are often safer because you let the garment cool and there's less risk of distorting it during peel. Peeling a film off a stretchy fabric while hot could stretch the fabric (and the not-yet-set ink) in unwanted ways, causing warping of the design. Cold peel avoids that by letting everything set. In practice, many find that a cold-peel, matte film that is thin works great on things like Lycra leggings — the design will flex with the material (and one can even press again with a silicone sheet to embed it a bit into the fibers). If using a hot peel on stretch fabric, you might only peel when it's warm and do it very carefully to avoid distortion. Key point: If you are doing sportswear or yoga pants (lots of stretch), invest in a known stretchable DTF film or at least a high-quality film with proven stretch performance. Also consider using a flexible additive in the adhesive powder as some suppliers suggest. The combination of a stretchy film, stretchy adhesive, and flexible inks will ensure even intricate logos won't crack when the fabric is pulled.
-
Blends and Other Fabrics: Blended fabrics (like poly/cotton blends, tri-blends, etc.), as categorized by the Fashion Institute of Technology, generally don't need a special film beyond what's needed for their primary components. If a film works on cotton and on polyester, it will work on a poly-cotton blend. The main consideration is often the weave and texture: e.g., heathered blends have a slightly textured surface, but DTF can handle that fine (the adhesive melts to flow into texture). For fabrics like denim or canvas, which are heavy cotton-based materials with rough texture, a cold peel film might be advantageous to ensure the adhesive cools and grips into the gaps of the weave. Films with strong adhesion (some advertise "strong adhesive layer" for tough fabrics) will shine here. Silk is a delicate fabric that actually can take DTF transfers too, but because silk is very heat-sensitive, you would use a lower temperature and definitely a cold peel (to be gentle). Some recommend using a cold peel film for silk specifically, to avoid any chance of fabric damage. Leather and faux leather can also be decorated; typically, a cold peel film at low temperature is used to not melt or discolor the material. For unique applications like caps and hats, see our DTF printing on caps and hats guide. In all these special cases, the general rule is: the more sensitive or textured the fabric, the more you lean toward a cold peel, high-adhesion film for a gentle but firm transfer. Conversely, for standard t-shirt material (cotton, poly, blends), you have the freedom to use whichever film type suits your needs (glossy/matte, hot/cold) since those fabrics are robust and easy.
Brand Examples (Maintaining a Neutral View): To illustrate how different brands tailor films to these needs, consider a few examples: STS (a well-known DTF supplier) offers a double-sided matte film that is positioned as a versatile solution for various fabrics. It's described as working on "spandex, polyester, denim, 50/50 blends, and more," providing long-lasting, vivid prints on all of them. This suggests a strong universal adhesive and coating that can handle both rough and stretchy materials. Another example is Color Prime's "Universal" film, which explicitly lists cotton, polyester, blends, and even nylon as suitable substrates. It emphasizes strong adhesion and durability to resist cracking on those materials. For quality control in your production, consult our DTF quality control checklist. On the other hand, Color Prime also has a "Quick Glide" (instant peel) film, illustrating a case where a manufacturer provides a hot-peel option aimed at speed and vibrant color output (useful for fast production on common fabrics). Kodak 's DTF film (Kodacolor FTF) is an example of a cold peel, glossy film that yields a matte finish on the garment and is noted to be anti-static and scratch-resistant, with transfers that stay vibrant through many wash cycles. Kodak highlights its rigorous testing on varied fabrics, from cotton to nylon, to ensure broad compatibility. Sublistar, another supplier, offers both cold and hot peel films and even a combined "hot & cold peel" product, often with an anti-static coating (especially on their double-matte versions to ease handling). They note that their films have "exceptional ink receptivity, anti-static and anti-blocking properties," which is important when printing large runs (films not sticking together or attracting dust). While each brand's marketing highlights certain strengths, the overall takeaway is that you should match the film's capabilities to your project's needs rather than any one brand being inherently superior. No single film is the "best" for everything – a film that excels in ultra-bright color on polyester might not feel as soft on a cotton hoodie, for example.
Practical Tips for Film Selection: In a professional DTF workflow, you might decide on a film type by asking a few key questions about the job: What fabric am I printing on? Does it require special handling (stretch, low heat)? Is output speed a concern or is maximum quality the priority? What kind of finish does the design or customer call for (glossy vs matte)? By answering these, you can choose the appropriate film category as we've outlined. For workspace setup considerations, see our DTF workspace setup guide. Always check the film manufacturer's instructions regarding compatible fabrics and wash tests. It's a good practice to keep sample swatches of different films applied on various fabric types; for instance, see how a hot-peel glossy transfer vs. a cold-peel matte transfer look and feel on a polyester jersey vs. a cotton tee. Such testing will reveal differences in color vibrancy (perhaps the glossy pops more on poly) and hand feel (matte might be softer on cotton). Regular printer maintenance is also crucial for consistent film performance. The right heat press technique complements proper film selection. In terms of scientific performance measures: look at a film's stated ink absorption (some list an ink load percentage – e.g., 300% or 400% – indicating how much ink saturation the coating can handle ), its thickness (thicker films ~100 micron may be easier to handle and more durable, whereas thinner ~75 micron films can give finer detail ), and any special coatings (anti-static back layer, etc.). According to the U.S. Occupational Safety and Health Administration (OSHA), proper handling and storage of printing materials is essential for workplace safety. Higher ink absorption means more vibrant, solid prints without bleeding, and a stable coating means repeatable results. For businesses looking to expand into specialty finishes, explore our guide on advanced DTF finishing techniques.
In conclusion, film selection in DTF is a balancing act between finish, peel method, and material compatibility. A glossy hot-peel film might deliver stunning, vibrant logos in record time for a batch of uniforms, while a matte cold-peel film might be the hero for a complex graphic that needs to last for years on a comfy cotton sweatshirt. Understanding these variations – glossy vs matte, cold vs hot peel, and specialized fabric-oriented films – allows you to make informed choices. By picking the right film for the job, you ensure better ink adhesion, optimal color brilliance, user-friendly application, durable results, and a transfer that is well-matched to the garment's fabric. This level of consideration elevates the quality of your DTF prints to a truly professional standard, which is the ultimate goal of the Iris DTF Academy training. For additional technical resources, visit Textile Research Institute or explore Mutoh's technical documentation. For those looking to start or grow their DTF business, explore our resources on DTF market research and DTF pricing strategies.