DTF Printer Maintenance & Troubleshooting Guide: Proven Routines to Keep Direct-to-Film Prints Flawless
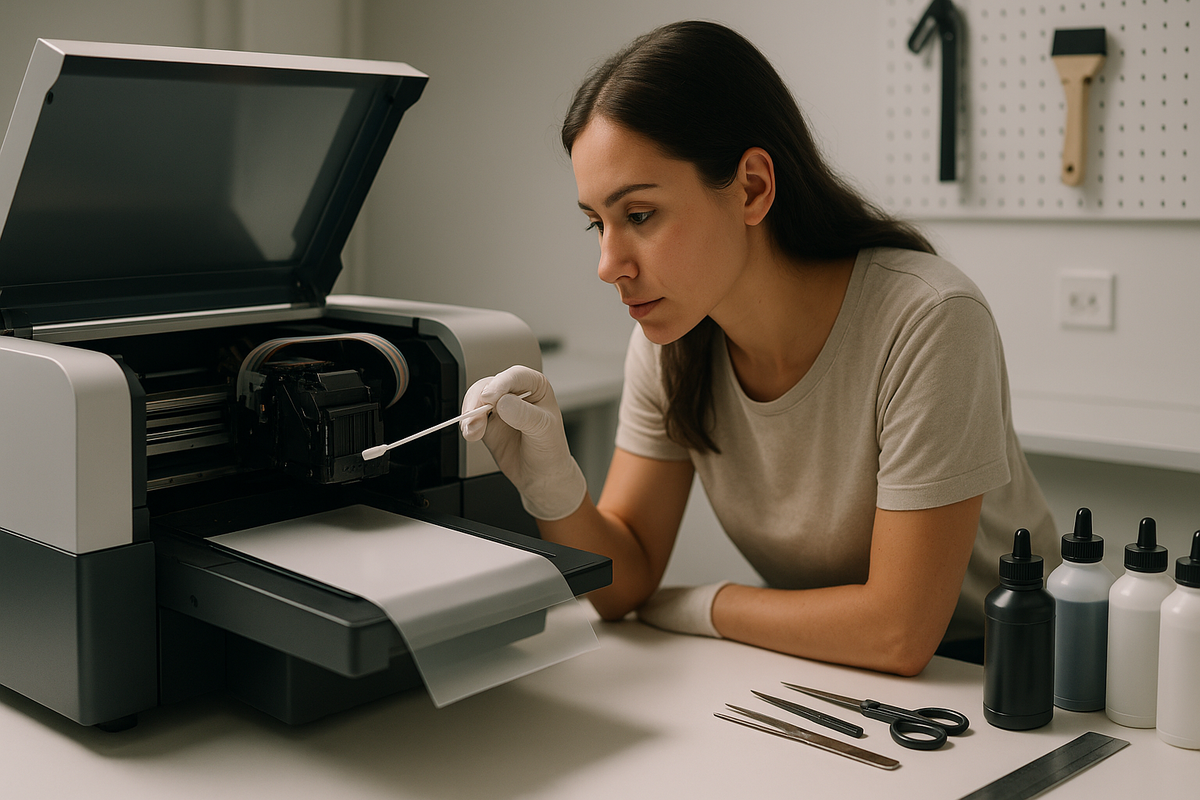
What Is This Article About?
Master intermediate DTF printer maintenance and troubleshooting. Prevent clogs, fix banding, and protect your investment for consistently flawless direct-to-film prints.
Direct-to-Film (DTF) printers require diligent care and troubleshooting to maintain consistent, high-quality output. This module (Topic 10 of Iris DTF Academy) builds on your basic DTF printing knowledge and guides you through intermediate maintenance tasks and common issue resolution. We will cover daily and periodic maintenance routines, diagnose frequent print quality problems, and outline preventative strategies to minimize downtime. The tone here is encyclopedic yet practical – providing detailed instructions in accessible language for those running professional DTF operations.
Essential Routine Maintenance Tasks
Regular maintenance is the cornerstone of reliable DTF printing. By performing certain tasks daily and weekly, you can prevent many issues before they occur. Below is a breakdown of essential routine maintenance tasks:
-
Daily Nozzle Check: Begin each day with a nozzle check test print. This quick diagnostic ensures all color channels (including white) are firing correctly. Only proceed with production if the test pattern shows at least ~90% of nozzles firing properly. If you see gaps or missing lines in the nozzle check, do not start a print job – address the issue first (usually by cleaning, as discussed below). Catching clogs early prevents defects like banding or color drop-out, a common issue discussed in our comprehensive troubleshooting guide.
-
White Ink Agitation: White DTF ink must be agitated daily. All white inks tend to settle and separate if left stagnant, as explained in our consumables guide. If your printer has an automated white ink circulation system, run it once each day. Otherwise, gently shake the white ink cartridges or stir the bulk ink tank to keep the pigment evenly suspended. Neglecting this will cause sedimentation that clogs lines and printheads. Tip: Even if the printer is idle, continue daily white ink agitation and maintenance – do not pause these routines, as stagnant white ink can quickly create clogs.
-
Capping Station Cleaning: At the end of every printing day, clean the capping station (the rubber cup where the printhead parks). Ink accumulations here can prevent a proper seal and lead to dried ink on the printhead. Using a lint-free swab and manufacturer-recommended cleaning solution, wipe away any wet or dried ink from the cap top. Do not use alcohol on the capping station's rubber parts, as it can dry them out or leave residue. Keeping the cap top clean ensures that when the head is parked, it stays moist and airtight, which is critical for overnight nozzle health. After cleaning, many technicians also fill the cap with a few drops of cleaning fluid and perform a "flush" or small cleaning cycle to draw the fluid through – this helps keep the cap and pump lines clear.
-
Printhead Wipe-Down: Gently clean around the printhead face daily to remove any ink mist or buildup. During printing, ink overspray and the action of the wiper blade can leave residue on the printhead perimeter. Using a lint-free swab with proper cleaning fluid, carefully wipe the printhead surface or edges without scratching it. Avoid harsh solvents like alcohol on the printhead nozzle plate or surrounding area – use only cleaning solutions approved for your printer, as mentioned in equipment guides from leading DTF equipment manufacturers. Regular wipe-downs prevent ink accumulation that could later flake or clog the nozzles. Note: Always perform printhead maintenance with the machine powered off and printhead parked or positioned per manufacturer instructions to avoid damage.
-
Wiper Blade Cleaning: The wiper blade is a small rubber squeegee that wipes excess ink off the printhead. If it's dirty or ink-encrusted, it can scratch or contaminate the printhead. Clean the wiper daily by moving it out (if the printer allows) or when the head is uncapped. Use a swab or soft cloth with cleaning fluid to remove ink residue from the wiper blade. A clean wiper is essential for effective nozzle cleaning – built-up gunk on the wiper will simply smear more ink onto the head. (Again, avoid alcohol on rubber parts to prevent drying or cracking.)
-
Check & Empty Waste Ink Bottle: Most DTF printers have a waste ink tank or bottle that collects flushed ink from head cleanings. Check this waste container daily and empty it before it overflows. An overfilled waste bottle can create back-pressure in the waste lines. If the waste ink tube end is submerged in an overfull bottle, it may siphon ink back toward the printhead, causing serious contamination. Never allow the waste ink tank to overflow or back up – this can ruin the printhead or electronics. Dispose of waste ink safely according to your supplier guidelines and EPA hazardous waste regulations, following safety standards from ASTM International.
-
Ink Level Check & Top-Up: DTF printers should not be allowed to run inks completely dry, as air can enter the lines and cause nozzle drop-outs. Check ink levels daily (many printers have sight windows or level sensors ) and top up cartridges or tanks as needed. Running out of ink mid-print can introduce air into the dampers and printhead, leading to clogs. Keep an extra set of ink on hand and never use expired or settled ink, which can cause printing issues (especially with white ink). Using only compatible, high-quality DTF ink will also reduce clogging risks. For proper inventory management strategies, maintain a buffer stock of essential consumables.
-
Maintain a Dust-Free Printer Area: Make it a routine to dust off and cover your printer at the end of the day. Use a clean, dry cloth to wipe any dust from the printer surfaces, and consider covering the machine with a breathable dust cover when not in use. Lint, dust, and textile fibers are notorious for sneaking into printers and ink systems. Dust on the encoder strip or in the capping station can cause sensor errors and clogs. A clean environment significantly reduces random print defects, as emphasized in our workspace setup guide. (We'll discuss environment control more later.)
-
Periodic Deep Cleaning: In addition to daily upkeep, schedule more thorough cleanings periodically. For example, weekly you might clean the encoder strip (the clear plastic strip that the printhead uses for positioning) by gently wiping it with a lint-free swab and a bit of isopropyl alcohol to remove any ink splatter. Also consider lubricating the carriage rail monthly or as needed – if you hear squeaking as the printhead moves, apply a small amount of manufacturer-approved grease on the rail to keep it moving smoothly. Always power off and unplug before any such maintenance.
-
Routine Part Replacements: Some maintenance components require replacement after a certain period. For instance, many operators replace the white ink filters every 3 months or so. These filters (often inline or within dampers) catch pigment particles and prevent clogs; replacing them regularly ensures smooth white ink flow. Similarly, waste ink pads (if your printer uses internal pads instead of a bottle) may need replacement or resetting periodically, and dampers or cartridges might be changed out a couple of times a year if you notice degradation in ink flow. While replacing parts can be more advanced, it's still preventative maintenance – we won't cover the full how-to here, but note these tasks for your maintenance schedule, which should be integrated with your quality control checklist.
By adhering to this maintenance checklist, you'll avoid most common DTF printer headaches. Daily care like nozzle checks and cleanings directly translates to consistent print quality and longer printhead life. Skipping routine maintenance, on the other hand, almost guarantees clogs and downtime. Make these practices a habit as you operate your DTF printer.
Common DTF Printer Issues & Troubleshooting Guide
Even with good maintenance, issues can occasionally arise. In this section, we'll explore common DTF printer problems – such as banding, missing colors, ink bleeding, and nozzle clogs – and how to systematically diagnose and resolve them. A methodical approach to troubleshooting will save you time and materials when something goes wrong.
Banding (Horizontal Lines or Streaks)
Symptoms: "Banding" refers to unwanted horizontal lines or stripes across the print, or areas of uneven color density. Bands may be white (no ink), or lighter/darker lines in solid colors. This issue is very common if any nozzles are clogged or misfiring.
Likely Causes: The number one cause of banding in DTF (and inkjet printing generally) is clogged or deflected nozzles. If certain printhead nozzles aren't firing, those lines of ink won't be printed, resulting in light bands across the image. Banding can also occur from inconsistent ink flow (e.g. if a damper is not delivering ink smoothly) or mechanical issues like the media not advancing properly. In some cases, incorrect print settings (resolution or pass count in the RIP software) can exaggerate banding if the printer isn't calibrated for them.
Troubleshooting Steps:
-
Run a Nozzle Check: As soon as you see banding, stop and print a nozzle test pattern. This will reveal if any color channel has missing lines. If you notice missing segments on the nozzle check, you have clogged nozzles – perform a head cleaning before printing further. It's ineffective to re-run the print hoping banding goes away; you must confirm all nozzles are firing first.
-
Clean the Printhead: If the nozzle check shows clogs, use the printer's cleaning cycle to clear them. Start with a normal (light) cleaning. After cleaning, run the nozzle check again to see if the gaps improved. It may take 1-3 cleaning cycles to recover all nozzles. Ensure you have adequate ink in the system during cleanings. If after a few attempts the same nozzles are still missing, consider a deeper approach: a manual nozzle flush or soak. For example, you can pause and place cleaning solution on the capping station and let the printhead sit on it for an hour to dissolve dried ink, or use a manual cleaning kit/syringe as per manufacturer instructions. Do not overdo cleanings – five or more clean cycles in a row without improvement may waste ink and indicate a stubborn clog that needs manual intervention (at that point, soaking the head with a cleaning fluid is recommended ).
-
Check Media Feed and Encoding: If the nozzle check is perfect (no missing lines) but you still see banding, the issue might lie elsewhere. Ensure that the film is being fed straight and not slipping. Clean the pinch rollers and grit roller to prevent any media feed skew or slippage. Also, wipe the encoder strip (a dirty encoder can cause the printer to misplace lines slightly). These mechanical checks can resolve banding that occurs despite clean nozzles.
-
Verify RIP Settings: As a final check, verify your RIP software settings for resolution, wave patterns, or passes. Banding can show if the print mode is set to too low a pass count for the given image/resolution. Additionally, ensure the ICC profile and calibration are correct if the banding is manifesting as color shifts rather than pure white gaps. In most cases though, a clean nozzle check means the printer is fine and true banding (as opposed to color profiling issues) should not occur; thus focus on mechanical and software alignment if clogs are ruled out.
Preventing Banding: Maintain your daily nozzle checks and cleanings – most banding is prevented by catching clogs early. Also, keep the printer in a suitable environment (temperature and humidity) controlled according to ISO standards to avoid drying out the ink in mid-print (dry conditions can lead to nozzles clogging during long runs). Regularly agitate inks and keep ink supply components clean to ensure consistent ink flow across the print width.
Missing Colors or Channels
Symptoms: In this scenario, one or more colors do not appear in the print at all, or certain elements print in the wrong color. For example, no white underbase is printing, or all prints have a color cast because cyan or magenta is missing. A nozzle check would show one color channel not firing any lines.
Likely Causes: A severely clogged printhead nozzle channel (or multiple channels) is a primary cause – e.g. if the white channel is completely clogged, you'll get no white ink on film. Missing colors can also result from an empty ink cartridge or failed ink delivery (air in the lines, a pinched ink tube, or a clogged damper that's not allowing ink through). In other words, anything that interrupts ink flow for a given color will make that color vanish from prints. Incorrect printer settings or job setup (using the wrong color profile or forgetting to enable the white layer in RIP) can be a cause, but here we focus on maintenance-related causes assuming your print settings are correct.
Troubleshooting Steps:
-
Nozzle Check & Ink Level: As always, start with a nozzle check pattern. If an entire color is missing on the test (e.g., no white grid printed), first inspect the basics: is the ink cartridge/tank for that color empty or very low? If so, refill it, run a head cleaning to pull the new ink in, and test again. If ink was plentiful, the issue is likely a clog or ink flow blockage.
-
Head Cleaning and Multiple Purges: For a single missing color, try a dedicated cleaning cycle targeting that channel (if your printer software allows, some have a powerful cleaning mode for just the missing color). You may need to do a "power cleaning" or manual ink purge. For instance, in stubborn cases you might use a syringe to gently pull ink through the dampers or push cleaning fluid in, then perform cleaning cycles. This can help remove air bubbles or clots in the ink line. Always follow manufacturer guidelines for any manual ink flush to avoid damage.
-
Check Ink Delivery Components: If cleaning doesn't restore the color, inspect the ink delivery system for that channel. Ensure the damper (if your printer uses dampers) for the missing color is full of ink and not full of air. A damper that has run dry or is clogged with sediment will prevent ink from reaching the head. Tapping the damper gently or re-priming it might be needed. Look at the ink lines for air bubbles; air bubbles can block ink flow and cause dropouts. Many printers have a vent on cartridges – check that any air vent is open (if a cartridge is completely sealed, it can create a vacuum stopping flow). Also verify that the capping station is properly wet and not causing that channel to dry out between prints.
-
Software Check: After hardware checks, double-check your RIP software settings as a sanity measure. Make sure you didn't accidentally turn off a color channel or that the design indeed contains that color. For example, if no white prints, ensure the RIP is set to generate the white layer and that you're not in CMYK-only mode, as covered in our artwork preparation guide. Similarly, if a color is consistently missing in output but your nozzle check is now good, it could be a profile or channel mapping issue in software.
Preventing Missing Colors: Many causes of missing colors are again tied to clogs or ink starvation. Preventative measures include regular stirring of inks (especially white) to avoid settled pigment clogs, and keeping ink delivery parts clean and replaced on schedule (filters, dampers, etc., before they get gummed up). Also, never let cartridges run completely dry – that's a fast track to pulling air into the system. If you must pause printing for an extended period, consider doing a flush or parking the printhead in cleaning fluid to prevent one channel from drying. Running a test print with a nozzle check pattern or a full-color test image every few days (if the printer isn't used daily) can keep all channels alive and catch any issue early.
Ink Bleeding or Smudging
Symptoms: The printed image on the film exhibits bleeding, smearing, or "pooling" of ink. Fine details might spread or halo out, and colors may run into each other. You might see wet-looking areas or mottled, blurry edges on what should be crisp artwork. This is observed on the film before transferring, indicating a printing issue (not to be confused with bleeding after transfer, which is another matter).
Likely Causes: Ink bleeding typically indicates over-saturation or improper curing of ink on the film. If too much ink is laid down for the film's coating to hold, it can puddle and bleed. This can happen due to incorrect print mode settings (e.g. using a profile that lays down excessive ink) or using a film that isn't properly compatible (cheap or wrong type of PET film whose coating can't absorb the ink). Another cause is high humidity or moisture on the film – if the film has absorbed moisture from the air, the ink might not adhere evenly and can bead up or spread unpredictably. Similarly, expired or separated ink (especially white) can cause consistency issues that lead to poor ink laydown. Finally, insufficient drying/curing (for printers with inline heaters) might leave the ink wet for too long, causing it to flow out before the adhesive powder is applied.
Troubleshooting Steps:
-
Check Print Settings: Verify that you're using the correct ICC profile or print configuration for your ink/film combination. If you recently changed ink brand or film type, you may need to recalibrate. Ensure the resolution and pass count are appropriate – higher passes or using a uni-directional mode can sometimes help if lowering the ink volume is needed. As a test, you can reduce the overall ink limits (some RIP software allow you to dial back ink density, especially for white) and see if the bleeding improves. If it does, you were likely over-saturating the film.
-
Inspect Film and Ink Quality: Make sure you are using a compatible film and quality ink. An incompatible film (or a bad batch of film with coating defects) can cause ink to puddle or not anchor well. Likewise, using non-DTF or low-grade ink can produce improper viscosity or drying times. Always use the film and ink combination recommended by your printer or ink vendor to ensure they work well together. If ink has been sitting on a shelf for too long, especially white ink, it might have partially separated or gone bad – try a fresh batch of ink to compare.
-
Control the Environment: Measure the humidity in your print room. The ideal environment for DTF is typically around 40-60% relative humidity and a moderate temperature (around 20–25°C), according to OSHA workplace standards. If humidity is too high, the film can attract moisture, leading to "sweating" where ink won't spread evenly. In a humid room, you may see an almost oily or wet look on prints because the moisture interferes with ink settling. Use a dehumidifier if RH is consistently above recommended levels. Conversely, extremely low humidity can cause ink to dry too quickly or even dry on the nozzle, but bleeding is more often a high-humidity or oversaturation issue. Keep your film stored in a dry container (with silica gel packs) to avoid it absorbing moisture.
-
Evaluate Curing and Workflow: If your printer has a built-in heater or you flash-cure the print before applying powder, ensure that process is dialed in. Wet ink will obviously smudge or bleed; some printers require an IR dryer or heated platen to partially cure the ink immediately after printing. If you see bleeding, perhaps the ink isn't getting any chance to set. Adjust the curing temperature or time slightly if possible (but not so much as to cure it fully, which would prevent powder from sticking). Additionally, check that you are applying powder promptly and evenly – leaving a wet print sitting too long before powdering could allow inks to bleed out. Work methodically: print, then immediately powder and cure as per guidelines.
Preventing Ink Bleed: Use proper settings and quality consumables from the start. Always match your RIP profile to the exact ink and film you use to avoid over-inking. Keep your printing environment controlled (many print shops run a dehumidifier in summer and a humidifier in winter to stay in the ideal range). Store your film in a sealed bag to keep it dry. Also, regularly maintain your white ink – separated or clumpy white ink can cause random blotches or inconsistent laydown, so daily shaking and using fresh white ink will help maintain uniform prints. If you consistently print a lot of heavy ink designs, it may be worth performing periodic head alignments and calibration prints to ensure the ink is landing precisely where it should, which can mitigate the appearance of any spread.
Nozzle Clogs and How to Clear Them
Symptoms: Nozzle clogs underlie many of the issues above (banding, missing colors). The symptoms of a clog specifically are seen in the nozzle check pattern – small segments or entire blocks missing for one or more colors. In prints, clogs show up as streaks, color loss, or graininess. You might also hear the printer "firing blanks" (no ink coming out) if a clog is severe.
Likely Causes: DTF inks are pigmented and can dry out if not kept in motion. Dried ink in the printhead nozzles is the immediate cause of clogs. This drying can result from irregular use (printer sitting idle), inadequate maintenance (nozzle left uncovered or cap dried out), or environmental factors (low humidity, high heat accelerating ink drying). White ink clogs are especially common because of the heavy titanium dioxide pigment – if not circulated, it settles and cakes in the lines/head. Air ingestion into the lines (from running a cartridge dry or a leak) can also cause clogs: ink can retract and leave dry residue in the head. Additionally, using subpar ink or mixing different ink brands can lead to pigment coagulation and clogs.
Troubleshooting/Resolution: Clearing clogs can range from simple to labor-intensive depending on severity:
-
Automatic Cleaning Cycles: Start with your printer's built-in cleaning feature. A normal cleaning flushes ink through all nozzles to dislodge minor clogs. Always do a nozzle check after cleaning to see if the clog improved. If a few lines are still missing, run another cycle. Most printers also offer a more powerful or "deep" cleaning mode – use this if two regular cleanings don't help. Keep in mind, multiple cleanings consume a lot of ink (and fill the waste tank), so it's a balance between persistence and over-doing it.
-
Manual Nozzle Flush: For clogs that persist after automatic cleaning, a manual flush can be effective. This involves using a cleaning solution specially made for printheads. One method is to wet cap the printhead: power off the printer, move the head off the cap station, place a few milliliters of cleaning fluid into the cap, and move the head back so the nozzle plate soaks in the fluid. Let it sit for 30 minutes to a few hours (some users let it sit overnight for very stubborn clogs). This soaking helps dissolve dried ink. Afterward, power on and run a cleaning cycle and nozzle check. Another method is using a syringe with a silicone tube to directly flush cleaning fluid through the printhead. This must be done very gently at low pressure to avoid damaging the nozzles. Follow a trusted procedure or manufacturer recommendation if attempting a direct flush. Never use excessive force – the goal is to dissolve the clog, not blast it out by pressure (which can blow out the nozzle membranes).
-
Nozzle Extraction (Pulling Ink): Sometimes pulling ink from below can help. If your printer's capping station has a pump, you can manually activate it or use a syringe on the waste ink line to draw ink through the head. By drawing a few milliliters out, you may pull the clog through. One guide suggests drawing ~3–5 ml from the ink lines or dampers and ~10 ml from the waste line, then performing a cleaning flush. Essentially, you're using suction to clear the blockage and bring fresh ink in.
-
Replace Suspect Components: If one particular channel keeps clogging repeatedly, consider that the dampers or filters might be partially blocked. Dampers have tiny mesh screens that can get clogged over time (especially with white ink). Replacing a damper or an inline filter for that channel can restore proper flow. Similarly, ensure the capping station is in good condition – a cracked or clogged cap top won't provide the necessary suction to clean the head, so clogs persist. You might need to clean or replace the cap top if it's not sealing well. (We won't delve into full part replacements here, but be aware these parts have lifespans.)
If after all these efforts a nozzle is still permanently clogged (no improvement in nozzle check), you might be dealing with a dried ink plug that just won't budge, or a damaged nozzle. At that point, it's often best to consult a technician or consider that the printhead may need replacement in the future (advanced repair outside the scope of this module). But usually, consistent maintenance will prevent clogs from ever getting to that irreparable stage.
Preventing Nozzle Clogs: Prevention is far easier than cleanup. Here are key strategies to avoid clogs in the first place:
-
Daily Maintenance: As already emphasized, daily nozzle checks and cleaning of the printhead, wiper, and cap keep clogs at bay. Never skip park/clean procedures at shutdown. After your final print each day, clean the head and cap, and ensure the head is capped with moisture (some users put a few drops of cleaning fluid on the cap to keep the head from drying overnight ). Keeping the printhead "wet" when not in use is vital.
-
Regular Ink Agitation: Make it a hard rule to shake your white ink every day (both the cartridge and any external bottles). Also shake color ink cartridges every week or so if they sit for long. This prevents sediment that can later get sucked into the head. Using printers with white ink circulation systems continuously (some have periodic stirring pumps) is ideal. If not, do it manually. Never let white ink sit in lines for many days without movement.
-
Print Often: Ironically, printing is a form of maintenance. If you let a DTF printer sit unused for a week, you are much more likely to encounter clogs. Try to run at least a small test print or nozzle pattern every 1-2 days. This keeps the ink flowing and fresh ink replenishing the head. Printers in daily use, with proper care, often have fewer clogs than those started up intermittently.
-
Environment Control: Keep the room at a moderate temperature and humidity. Low humidity (below ~45%) will dry out nozzles quickly, so use a humidifier to stay in a safe zone. But also avoid extremely high humidity which can affect ink (aim for a stable, moderate environment). Also, avoid direct drafts on the printer; air conditioners or heaters blowing directly can dry the head on one side. And as mentioned, a dust-free environment prevents foreign particles from contributing to clogs.
-
Use Quality Ink and Consumables: Cheap or inconsistent inks can have pigment particle size issues or improper formulation leading to more clogs. Use reputable DTF inks and avoid mixing brands if possible. The same goes for cleaning solutions – use solutions made for your printer or ink type (generic cleaning fluids might not dissolve your ink effectively, or worse, could damage components). Follow the manufacturer's maintenance guidelines on cleaning frequency and part replacement. With these practices, nozzle clogs will be rare, and when they do occur, they'll be minor and easily cleared.
Preventative Maintenance Strategies to Minimize Downtime
Preventative maintenance is a proactive plan to keep your printer running smoothly, rather than reacting to problems after they occur. By sticking to a maintenance schedule and implementing best practices in your workflow, you can minimize unexpected downtime and extend the life of your equipment. Below are key strategies for preventative care that successful DTF businesses implement:
-
Establish a Maintenance Schedule: Create a checklist and calendar for daily, weekly, and monthly maintenance tasks (many of which we detailed earlier). For example, daily: nozzle check, clean head/wiper/cap, shake inks, etc.; weekly: deeper clean of caps and rollers, verify firmware or software updates, light lubrication; monthly: inspect/replace dampers or filters, clean ink tubes, etc. Having a schedule ensures nothing is forgotten. Sticking to routine tasks prevents unexpected failures – it's far better to clean a little each day than to deal with a major clog or breakdown later. Integrate this schedule with your staff training program to ensure consistency.
-
Control Temperature and Humidity: As part of your preventative plan, maintain the print room environment. Keep temperature around room temperature (around 20–25°C). Cold temperatures can thicken inks and hamper flow, while high heat can accelerate drying in the head. Humidity is even more crucial – aim for a relative humidity of 50-60% for optimal results. If your climate is dry, use a humidifier to keep humidity above 50%. This helps inks flow and prevents them from drying on the nozzles. If you're in a very humid area, ensure you have air conditioning or a dehumidifier to prevent moisture issues (though clogs are more associated with low humidity, very high humidity can affect print quality as discussed). Many serious DTF print shops invest in a hygrometer (humidity meter) and thermometer in the printer area to continuously monitor these conditions. Consistent environment = consistent performance.
-
Proper Startup and Shutdown Procedures: How you turn the printer on and off each day matters. In the morning, do a controlled startup – allow the printer to initialize, then perform a cleaning and nozzle check before printing to catch any issues. During operation, avoid turning the printer off and on unnecessarily (some machines perform a cleaning cycle at each power-on, which uses ink and wear). At the end of the day, always follow a shutdown routine: finish any pending jobs, clean the necessary components (head, cap, wiper), ensure the printhead is parked in the capping station properly, then power down safely. Never kill the power while the head is uncapped or moving. Some printers have a specific shutdown cleaning routine – use it. A proper shutdown ensures the printhead is sealed on a moist cap, preventing overnight drying.
-
Scheduled "Wet Capping" or Soaking: As a preventive measure, some users periodically do a longer head soak (for instance, on weekends if the printer will sit idle). This involves placing cleaning fluid in the cap and letting the head sit on it for an extended period (several hours) to keep everything hydrated and dissolve any starting buildup. While daily head soaks aren't necessary if all is well, doing an overnight soak once a week or so can be beneficial especially for white heads. It's like a deep conditioning for your printhead to counteract any slow accumulation of ink residue.
-
Monitor White Ink Sedimentation: We've mentioned it multiple times, but that's because white ink is the troublemaker if neglected. As a preventative step, incorporate white ink maintenance into your schedule: shake white ink bottles or cartridges at least once every day, and even during the day if the printer has been idle for hours. If your printer has a circulation pump for white, schedule it to run periodically (some printers allow you to set an automated cycle every X hours). Also, flush the white ink lines or replace white filters at set intervals (e.g. every 3 months as recommended), before a severe clog happens. This preemptive replacement of filters ensures you remove sediment before it reaches the head.
-
Periodic Preventative Replacements: Don't always wait for parts to fail. Certain consumable parts (capping station caps, wiper blades, dampers, filters, even o-rings in the ink supply) can be swapped out on a schedule. For instance, you might replace the capping station rubber yearly or sooner if you notice wear – a fresh cap will maintain better suction for cleanings. Replacing dampers every 6-12 months (or at least the white ink damper that sees the most sediment) can prevent slow ink flow issues. Keep a maintenance kit of these small parts so you can do a swap during scheduled downtime instead of when an emergency hits. Always log when a part was changed, to anticipate the next time. Factor these replacement costs into your pricing calculations.
-
Keep Firmware/Software Updated (Cautiously): While we won't dive into firmware updates in detail (that's an advanced topic), note that manufacturers sometimes release improvements that fix known issues (for example, better cleaning routines or error handling). As part of preventive care, you could check periodically if your printer model has updates – but always follow guidance and only update if you're confident it addresses an issue, since a failed firmware update can itself cause downtime. For now, focus on mechanical maintenance; software optimizations can be explored in a future module.
In summary, preventative maintenance is about consistency and foresight. Treat your DTF printer like a production machine that needs regular service, much like a car. A little time spent each day and week on maintenance dramatically reduces the chance of being stuck in the middle of a big order with a printer that won't print. By maintaining a stable environment, following procedures, and replacing parts before they completely fail, you'll ensure maximum uptime and reliable performance.
Maintaining the Ink Delivery System and Print Environment
Beyond the printhead and nozzle plate, the rest of the ink delivery system also requires care. The ink path—from cartridges or bulk tanks through tubes, dampers, and finally into the printhead—must remain clean and unobstructed. Additionally, the surrounding environment should be conducive to clean printing. Here we outline best practices for keeping the ink delivery system in top shape and maintaining a dust-free environment for your DTF printer.
-
Ink Cartridges and Tanks: Keep your cartridges/tanks clean and properly sealed when in use. If you use refillable cartridges or an ink tank system, avoid letting sediment collect at the bottom. Some large DTF setups have stirring mechanisms in the bulk tanks (especially for white); ensure those are functioning. When refilling cartridges or tanks, work cleanly to prevent introducing contaminants. Also, use high-quality ink to avoid debris or improper particle sizes that can clog the system. If you ever switch ink brands, flush the system before adding new ink to prevent any incompatible mixing that could gel the ink. Store spare ink in a cool, dry place with caps tightly on; do not expose ink bottles to extreme heat or direct sun which can spoil the ink.
-
Ink Lines and Hoses: The tubes that carry ink can develop residue over time, particularly the white ink line. Inspect the ink lines periodically – they should look full of liquid ink with perhaps a little air at top, but not large air gaps or obvious sludge. If you see ink pigment settling in a line (e.g. white ink separating out), it's a sign you need to circulate or flush. As a maintenance step, you can flush the lines with cleaning solution occasionally (this can be done by drawing cleaning fluid instead of ink through, during an ink change for instance). At least once a month, consider cleaning the white ink tube and pump if your printer design allows. This might involve flushing the line with cleaning fluid and running the pump to push fluid through. Be sure to follow your manufacturer's procedure, as disassembling tubes incorrectly can cause leaks or require re-priming. Keeping lines clean and free of air ensures consistent ink supply and pressure.
-
Dampers (Ink Filters): Dampers (also called ink filters or ink sacs) sit between the ink lines and the printhead on many printers. They serve to regulate ink flow and often have a fine mesh that filters out impurities. Over time, dampers can clog or the mesh can become blocked with pigment (white ink again being the usual suspect). A sign of a bad damper is if a specific color frequently goes out even though the cartridge is full and head is okay – the damper isn't delivering ink steadily. The best practice is to replace dampers periodically (e.g. every 6 months, or sooner if you notice issues). They are relatively inexpensive parts. Also, ensure the o-ring seals on the dampers (if any) are in good condition to prevent air ingress. When installing new dampers, fill them with ink (prime them) so you don't introduce air.
-
Capping Station and Pump: The capping station and the associated pump (which draws ink through the cap during cleaning) are critical to the ink delivery during maintenance cycles. Keep the cap top clean and moist as discussed, and also check the waste ink tubes for any kinks or blockages. If you notice that head cleanings aren't drawing ink (for example, nozzle check doesn't improve at all, and you don't see waste ink being produced), the cap or pump might be clogged. You may need to flush the pump system or even replace the cap top rubber if it's worn out. Part of intermediate maintenance could include using a syringe to gently push cleaning fluid through the cap and out the waste tube, clearing any clogs in that path. Ensure the waste ink lines are securely routed to the waste bottle with no sharp bends.
-
Keep it Dust-Free: Environmental dust control cannot be overstated. DTF printers have open ink paths and moving parts that can attract dust and lint (especially if you're printing on textiles nearby). Dust that enters the ink cartridges or lands on the film during printing can cause defects and clogs. To minimize this, maintain a clean room around the printer: regularly vacuum or wipe surfaces to reduce dust, but avoid kicking up dust while the printer is printing. It's wise to keep the printer area separate from where you handle fabric lint or powders, if possible. As mentioned earlier, cover the printer when not in use, but make sure the cover doesn't touch any wet parts or cause condensation. If your environment is inherently dusty (e.g. a garage or industrial setting), consider an air purifier in the room to capture dust, following NIOSH indoor air quality guidelines. Also, clean the printer's fans and vents if it has any, since clogged air vents can cause the electronics or printhead to overheat or not get proper airflow.
-
Static and Debris: In dry environments, static can cause dust to cling and can also attract fine fibers to the printhead. You might consider anti-static measures (some high-end setups use anti-static bars or mats near the printer). At minimum, keep the area around the printer free of loose threads, paper bits, or powder overspray. After powdering transfers, clean up any excess powder so it doesn't float around and potentially land in the printer mechanisms.
-
Handling Consumables: Store your DTF film and adhesive powder properly to avoid contamination. Keep film sheets in a bag or box to prevent dust settling on the printable side – any speck on the film can result in a white dot or void in the final print. Similarly, keep the powder container closed when not in use, and work with powder away from the printer's immediate vicinity so particles don't get onto the printhead or carriage. A little housekeeping goes a long way in preserving print quality.
By maintaining the entire ink delivery system – from ink bottle to printhead – and a clean environment, you ensure the printer can do its job without obstruction. Think of the ink path as the bloodstream of your printer: if there's gunk or clots in it, the printer will suffer. Regular cleaning, part replacements when needed, and a dust-controlled setup will keep the ink flowing smoothly and your prints looking their best.
Interpreting Printer Diagnostic Tests and Status Reports
DTF printers, like all inkjets, provide diagnostic tools to help you understand their health and performance. Knowing how to interpret status reports and test prints allows you to catch issues early and fine-tune the printer for optimal output. Here we'll discuss the key diagnostic print tests and what information you can gather from them, as well as monitoring printer status indicators.
-
Nozzle Check Test: This is the fundamental diagnostic print. It usually prints a small grid or pattern for each ink channel (CMYK and White). When you print a nozzle check, examine it under good light. All lines or patterns should be complete with no breaks. If you see any broken lines, that indicates which color has a clog or misfiring nozzles. The location and number of missing segments can help – for example, if only a few random breaks appear in one color, it's a minor clog that a cleaning should fix. If an entire section is missing, that channel might be completely clogged or not getting ink (as covered in troubleshooting). Some advanced RIP software might even quantify nozzle check results (e.g. "88% nozzles firing"). As a rule of thumb, ensure nearly all nozzles are firing (90%+ as suggested by some experts ) before doing high-quality prints, or you risk banding or color shifts. Use the nozzle check as a quick daily "status report" of the printhead – it's the first thing to look at to diagnose print quality issues.
-
Head Alignment Test: Many printers offer a printhead alignment utility that prints patterns (often a series of lines or boxes) to help you adjust bi-directional alignment or paper feed step. If you observe ghosting, shadowing, or color channels not perfectly overlapping, an alignment test can diagnose this. The printer will print sets of lines and you typically pick which lines are best aligned. By calibrating alignment, you ensure that when the printhead makes multiple passes, the dots line up correctly and you get sharp images. Run an alignment test if you see fuzziness in prints that isn't explained by clogs or media issues. Interpreting it is straightforward: follow the printer's instructions to choose the aligned patterns (usually, you input a number corresponding to the straightest line). This is more of a maintenance calibration than troubleshooting a "failure," but it's an important diagnostic print, especially after any mechanical changes (like if you removed and reinstalled a printhead or if the printer was shipped/moved).
-
Ink Status and Alerts: Most DTF printers (especially those based on Epson engines) have some form of status monitor software or control panel that reports ink levels, error messages, and maintenance tank status. Keep an eye on ink level indicators – if the software shows a cartridge is low, plan to refill or replace it before it actually runs dry. Also pay attention to any warnings like "Ink cartridge not recognized" or "Ink low"; these need immediate addressing to avoid print interruption. Another critical alert is for the waste ink tank or pad – many printers have an internal counter that triggers a "service required" message when the waste ink pad is near full. If your printer says maintenance required or that a waste reservoir is full, do not ignore this. Continuing to print can lead to messy overflow. Instead, replace or reset the waste ink pad/tank per the manufacturer's instructions (or have a technician do it). Interpreting status reports is often as simple as reading the messages: they're telling you something needs attention (ink out, cover open, paper jam, etc.). Always resolve any error state before attempting to print again.
-
Printhead Usage Reports: Some RIP software or printer utilities provide information like how many prints or how many cleaning cycles have been done, or ink consumption reports. These can be useful for long-term maintenance planning. For instance, if you see that you've done an abnormally high number of cleanings for one color, that might hint at an ongoing issue in that channel (like a leaky damper or bad cap causing frequent clogs). Ink consumption data can reveal if one channel is using ink too fast (perhaps due to a slight leak or purge issue). While these reports are more about overall monitoring, reviewing them periodically can give insight into whether your maintenance routines are effective. For example, if after implementing better humidity control you notice your monthly cleaning cycles count dropped, that's a good sign your preventive measures are working.
-
Test Prints for Quality: Aside from formal diagnostic patterns, sometimes the best test is to print a standardized image that contains fine text, gradients, and color patches. Keep a "reference print" file handy that you can output when you suspect an issue. By comparing how this test print looks now versus when things were working perfectly, you can spot subtle problems. For instance, print a gradient in each color – do you see smooth progressions or are there sudden jumps (could indicate a clogged nozzle in mid-density)? Or print a small text at 4pt size – is it legible and crisp (if not, maybe alignment or slight defocus of head)? These kinds of subjective tests complement the nozzle check by revealing issues you might notice in real designs. When interpreting such prints, you're looking for any deviations from the norm: unexpected lines, color shifts, blurriness, etc., then tracing those back to the likely cause (mechanical, head, or software). Consider creating test prints for your portfolio to showcase your print quality standards.
-
Error Codes and Logs: If your printer provides error codes (like some Epson-based DTF units might blink specific LED sequences or display codes on a panel), have the user manual's troubleshooting section available. An error code could pinpoint a specific fault (for example, "Error 0x10" might mean a carriage motor jam, as per the OEM documentation). Interpreting these is case-by-case; the manual or a support knowledge base will translate the code to a description. In general, any time the printer stops with an error, take note of what the code or message is. It's part of the diagnostic info. Sometimes simply power-cycling clears a transient error, but if it repeats, you'll need to address the underlying issue as indicated.
-
Software Diagnostics: Some printers or RIPs have utilities to do things like check nozzle health via software algorithms or to perform a purge pattern across the page to see consistency. Use these as needed – for example, a "purge pattern" is basically a flush print of all colors across the film. If you run that and see one color fading out toward the end, it might indicate an ink starvation issue (like a clogged vent or low ink not keeping up). These prints also help confirm if a clog is completely cleared: after a successful cleaning, a purge pattern should show uniform, solid bands of each color with no breaks.
In summary, make full use of the diagnostic tools your printer provides. The nozzle check is your first and most frequent diagnostic – treat it like the vital sign check for your printer's health. Alignments and test images help fine-tune quality. And status monitors or error messages should never be ignored; they are the printer communicating its needs. By interpreting these signals correctly, you can quickly direct your maintenance efforts to where they're needed and keep your DTF printer producing top-notch results with minimal downtime.
By mastering intermediate maintenance and troubleshooting, you're investing in the longevity and reliability of your DTF printer. Consistent upkeep ensures that mechanical issues, clogs, and environmental factors have minimal impact on your production. When issues do arise, systematic troubleshooting – backed by the diagnostic tests and practices covered here – will allow you to pinpoint and resolve the problem efficiently. With these skills, you'll be well-prepared to run a professional DTF operation that delivers high-quality prints day in and day out, without the printer itself becoming a bottleneck. For tips on optimizing the next step in your workflow, check out our heat press guide. Happy printing, and remember: a well-maintained printer is key to a successful DTF business!
Continue Your DTF Education
Enhance your maintenance expertise with more advanced guides at Iris Academy:
- DTF Color Management: Advanced Artwork & ICC Profiles
- Mastering DTF Adhesive Powder: Complete Application & Curing Guide
- DTF Heat Press Guide: Mastering Pressure, Temperature & Time Settings
- Specialty Inks & Finishes: Advanced DTF Techniques
- Common DTF Pitfalls: Ultimate Troubleshooting Solutions
Stay updated with the latest maintenance innovations through industry publications like Impressions Magazine and Printwear Magazine, and connect with professionals at FESPA events.