DTF Heat Press Guide: Optimal Pressure, Temperature & Time Settings
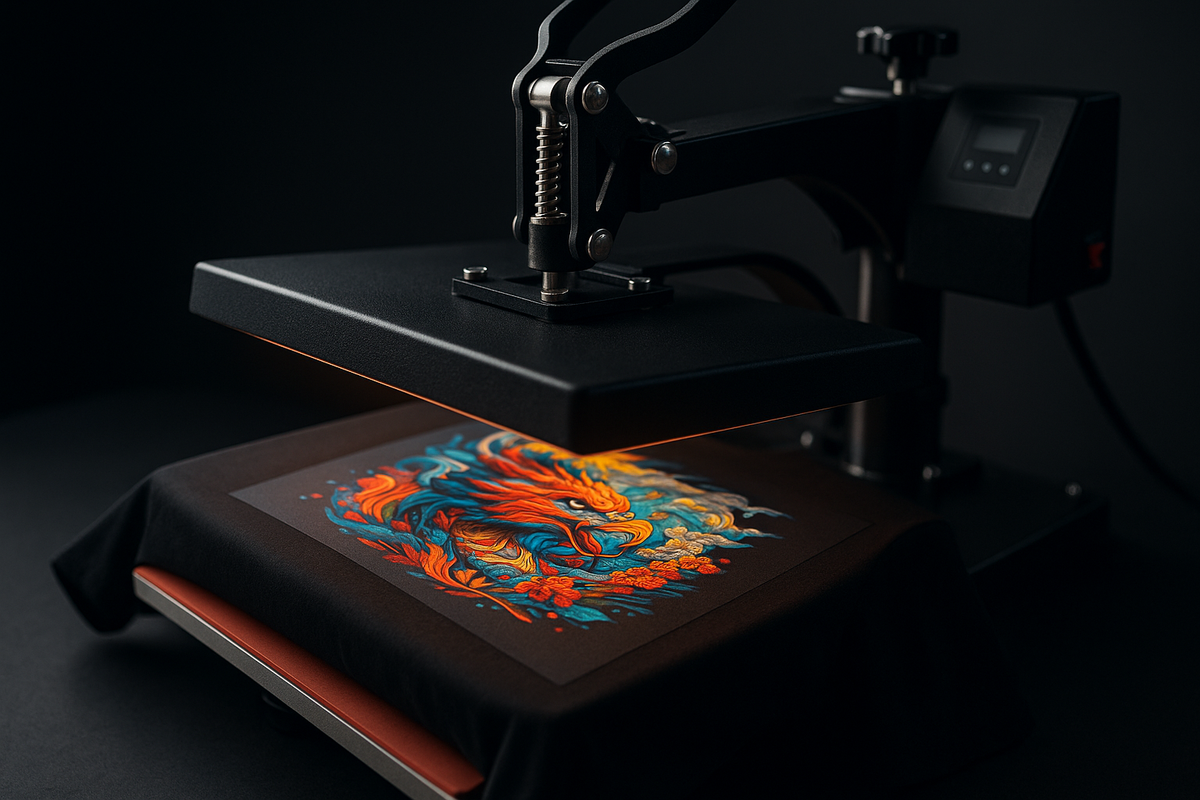
What Is This Article About?
Master perfect DTF transfers with the right heat press type, pressure, temperature and time—plus pro tips and quick fixes for scorching, peeling and more.
In this module, we dive into the heat press stage of Direct-to-Film (DTF) printing. We'll explore different types of heat presses used for DTF, how pressure/temperature/time settings affect transfer quality on various fabrics, the role of hot vs. cold peel films, troubleshooting common issues, and pro tips for consistent results in batch production. By the end, you should understand how to optimize your heat press technique to achieve durable, high-quality DTF prints.
Types of Heat Presses for DTF Transfers
Different heat press designs offer varying advantages in pressure consistency, ease of use, speed, and safety. Here we discuss five common types and their pros/cons for DTF:
- Clamshell Heat Presses – A clamshell press opens on a hinge like a clamshell, with the top platen lifting straight up at an angle. These are among the most popular presses for garments due to their simplicity and compact footprint. Advantages: Clamshells are generally affordable, lightweight, and space-saving – great for small workshops. They're easy to operate with a simple lever action and quick to heat up, enabling fast pressing cycles. Limitations: Because of the rear hinge, very thick items may not receive perfectly even pressure (the platen closes at a slight angle). Placement of transfers can be a bit tricky in the limited opening, and rigid clamshell platens carry a slight risk of scorching or leaving indentations on certain fabrics. In terms of safety, one must be cautious reaching under the hot upper platen since it hovers close to the lower platen when open. Modern clamshell models often include features like digital controls and auto-open mechanisms to prevent over-pressing, but fine pressure adjustments or pressure gauges are usually limited on basic models.
- Swing-Away Heat Presses – A swing-away press has a top platen that lifts vertically and swings completely to the side, away from the bottom platen. Advantages: This design gives full access to the garment/loading area, making it easier to position transfers accurately without the heat platen in the way. Swing-away presses apply very even pressure, even on thicker items, because the platen comes straight down uniformly rather than at an angle. They also reduce the chance of accidental burns when positioning a garment, since the heating element is moved off to the side (no hot surface directly above your hands). Limitations: Swing-away machines tend to be heavier and more expensive than clamshells, and they require a wider workspace because the top arm swings out (wider footprint). The swinging action adds a small extra step to each press cycle, so pressing might be slightly slower compared to a clamshell. Overall, swings are favored for their versatility (they can handle thicker substrates and uneven items easily) and safety, at the cost of space and price.
- Draw (Slide-Out) Heat Presses – A draw press, sometimes called a drawer heat press, combines elements of clamshell and swing designs. The upper platen typically still opens upward (often in a clamshell fashion), but the lower platen pulls out like a drawer toward the operator. Advantages: By sliding the lower platen out, you can lay out your garment fully outside the heat zone, similar to a swing-away's benefit. This provides a heat-free workspace for safe, easy positioning of the transfer. Draw presses often have a relatively limited footprint (you need clearance in front, but not to the side) – offering a "best of both worlds" solution for tight spaces. They are also fast to operate: you quickly pull the pallet out, arrange the item, then push it back in to press. Many draw presses apply very even pressure across the platen and support good alignment, since you can view the garment straight on. Limitations: The main downside is cost – the sliding mechanism and sturdier build make them pricier than basic presses. Mechanically they are a bit more complex (more moving parts), so maintenance can be slightly higher. Still, their greater versatility and operator safety/comfort make them popular for serious DTF shops willing to invest.
- Pneumatic Heat Presses – Pneumatic presses use air pressure (from an air compressor or built-in pump) to close the platen and apply force, rather than a manual lever. They can be clamshell or swing style in form, but the key is automated pressing with consistent pressure. Advantages: Pneumatic presses provide extremely consistent and adjustable pressure – you can dial in a specific PSI, and the machine will maintain that force evenly across the entire platen. This is excellent for DTF, where uniform pressure helps achieve reliable adhesion on every print. They also greatly reduce operator fatigue and variation; with a foot pedal or two-hand safety switch, the press closes itself with no physical strain. This automation often shortens each work cycle, increasing production speed for high-volume operations. Many pneumatic models also have auto-open and even auto-swing features, streamlining the workflow. Limitations: The upfront cost is higher, and you need an air compressor hookup (which can be noisy and add maintenance). They are usually heavy, industrial machines (less portable). In terms of safety, most are designed with features like two-button triggers or safety sensors because they close with significant force. Used properly, they're safe and even ergonomically beneficial, but you must ensure no obstructions (or hands) are in the way when the platen comes down. Pneumatic presses are ideal for high-volume production environments, offering repeatable results with minimal effort.
- Automatic Shuttle Presses – For the fastest production, some large DTF print shops use dual-station or shuttle heat presses. These machines have two lower platens and either one or two upper heating platens that automatically shuttle between them. For example, in a dual-shuttle press, you can be loading a garment on one platen while the other is being pressed, then the heat platen slides over to press the next one in an alternating cycle. Advantages: This design nearly doubles throughput by eliminating downtime – as soon as one item is done, the heat head moves to the next, allowing continuous operation. Pressure and temperature on these units are very precise (often pneumatic or electro-mechanically controlled), ensuring top-notch consistency even across hundreds of prints. They are often equipped with digital controls, programmed recipes, and safety lockouts for reliable, repeatable performance. Limitations: Shuttle presses are expensive and consume more space. They may require dedicated power circuits (and air, if pneumatic) and are generally stationary pieces of equipment. Setup and training are a bit more involved. From a safety perspective, the moving platen or shuttle system will have guards or require the operator to activate the cycle with hands clear. When used correctly, they can actually improve safety by reducing manual handling of the hot platen. In short, automatic shuttle presses are ideal for large batch production, where their efficiency outweighs the cost – they deliver the highest production speed with consistent quality, but are overkill for small-scale use.
The Key Heat Press Settings: Pressure, Temperature & Time
Achieving a high-quality DTF transfer is all about finding the right combination of pressure, temperature, and time. These three variables work together to properly melt the adhesive powder and bond the printed film to the fabric. An imbalance in any of them can lead to subpar results, so it's important to understand their roles:
-
Pressure: Adequate pressure ensures the transfer film makes firm, even contact with the garment, allowing the molten adhesive to penetrate the fabric fibers. DTF transfers generally call for medium to firm pressure across the whole design. If pressure is too light, parts of the design may not adhere (you'll see areas peeling or not fully bonding). If pressure is too high, you risk compressing or squishing the inks/adhesive which can affect print texture, and you might also leave a platen imprint on the garment. Different presses allow pressure setting in different ways – many manual presses use a knob that you tighten for more force (with experience, you learn what "medium" or "firm" feels like), while pneumatic presses let you set a PSI value. Also consider fabric thickness: a thicker item (like a hoodie) effectively needs a higher pressure setting or adjustment compared to a thin T-shirt to achieve the same force at the print surface. In all cases, aim for pressure that is evenly distributed across the platen. Uneven pressure can cause one side of a transfer to lift – it's crucial that your press is level and that any seams or buttons are padded so the design area gets uniform pressure.
-
Temperature: The heat level of the press must be hot enough to melt and activate the adhesive on the DTF film, but not so hot that it scorches or damages the fabric. Most DTF adhesive powders melt in the range of ~270–325°F (132–163°C), so you will typically press between 300°F and 350°F depending on the material. In general, cotton fabric can handle and often requires higher temperatures (around 325–350°F) to ensure a good bond, whereas polyester or delicate blends should be pressed at the lower end of the range (280–300°F) to avoid scorching or dye migration. Always follow the transfer manufacturer's recommended temperature if provided, as some DTF films are formulated for low-temp application. It's wise to use an infrared thermometer or heat strips to verify your press's actual platen temperature, since an inaccurate thermostat can throw off your results. Keep in mind that too low a temperature (even if you press longer) may fail to fully melt the glue, leading to poor adhesion, and too high a temperature can singe the fabric or cause the print to become brittle. Finding the "sweet spot" (usually in the low-300°F range for DTF) is key for vibrant, long-lasting prints.
-
Time (Dwell Time): The press time is the duration for which heat and pressure are applied. DTF transfers bond very quickly relative to some other methods – typically around 10 to 15 seconds of press time is sufficient in most cases. Within this window, the adhesive melts and interlocks with the garment fibers. Pressing too short can result in incomplete adhesion (parts of the design might stay on the film or peel off easily), while pressing for too long can cause the print to start degrading – extended heat might make the ink layer overly soft or cause it to crack as it cools. It's a good practice to stick to the recommended time from your transfer supplier; common guidance is about 12 seconds at medium pressure as an ideal balance for DTF. If you're unsure, start with around 12 seconds and adjust if needed based on results. There is a bit of leeway (for example, pressing 15 or even 20 seconds likely won't "burn" a DTF transfer, but beyond the ideal time you get diminishing returns or potential issues ). Always use a timer (most presses have one built-in) to ensure consistency, especially when doing multiple pieces.
In summary, all three factors – pressure, heat, and time – must work in harmony to produce a quality DTF print. If you notice an issue (like peeling edges or a scorch mark), revisit these variables: you may need to increase or decrease one of them slightly. A good practice is to do test presses when you change to a new fabric or batch of transfers. Dial in the settings on a scrap or test garment before committing to an entire production run. Once you find the optimal settings for a particular material (for example, a certain brand of T-shirt), record those settings. Next, we'll look at how different fabric types might require tweaking these parameters.
Recommended Press Settings by Fabric Type
One of the big advantages of DTF is that you can apply transfers to almost any fabric type (cotton, polyester, blends, nylon, etc.). However, you will get the best results if you adjust your press settings to suit the fabric. Here are some fabric-specific guidelines for DTF transfers:
-
100% Cotton: Cotton is durable under heat and can be pressed at higher temperatures. A typical setting for DTF on cotton is around 325°F to 350°F (163°C to 177°C), pressed for 10-15 seconds with medium-firm pressure. The higher heat helps the adhesive really anchor into the cotton fibers, ensuring strong adhesion. Always pre-press cotton garments for a couple seconds to remove moisture, as cotton can hold humidity that might interfere with the transfer. You shouldn't see scorching on cotton at 330°F for 12 seconds, but if you go towards 350°F or above, be cautious with time (stick closer to 10 seconds or use a press cloth). Heavier cotton (like fleece hoodies) might need a bit more pressure or a couple extra seconds due to thickness. Peel the film according to its instructions (hot or cold) – cotton itself can handle either peel method fine.
-
100% Polyester: Polyester (and poly-rich blends) are heat-sensitive. High temperatures can cause scorch marks (brownish discoloration) or a permanent heat gloss/sheen on polyester, and in dyed poly fabrics you risk dye migration (the fabric color bleeding into the print) at excessive heat. Therefore, use a lower temperature for polyester DTF transfers: typically 280°F to 300°F (138°C – 149°C) is recommended, and never more than about 320°F for most poly garments. You may need to press slightly longer at the lower temp; for instance, 12-15 seconds at 285°F is a common setting to get full adhesion without scorching. It's extra important to ensure medium-firm pressure with poly, since you're using less heat – the pressure helps the adhesive bond. Light-colored or white polyester can actually handle higher heat without visible scorch, but dark poly (especially navy, black, red) will often develop a shine or color change if pressed too hot. So err on the side of caution. Using a silicone parchment or a Teflon sheet on top can help avoid direct contact and reduce heat marks on polyester. Also, let poly cool a bit before peeling even if using "hot peel" film, as peeling very hot can sometimes provoke color distortion in the fabric. In short, low and slow(er) is the way for polyester: it will still bond great if you give it the proper time at a lower temp.
-
Cotton-Poly Blends: Blended fabrics (50/50 T-shirts, poly-cotton hoodies, etc.) fall in between. A safe starting point is about 320°F (160°C) for ~12 seconds with medium pressure. Because blends have polyester, you should watch for scorching if you go much above 330°F. Many find around 315°F for 15 seconds works well on common 50/50 blend tees – hot enough for the cotton content, but gentle enough for the poly. If your blend garment has a low poly percentage (say 80% cotton, 20% poly), you can treat it more like cotton; if it's high poly (e.g. triblends with 65% poly), treat it more like full polyester with lower temp. The range of 300–350°F often cited for blends reflects this spectrum. When in doubt, use the cooler end of the range and only increase temp if you notice adhesion issues. Blends generally press nicely and you can use standard DTF settings; just be mindful that some fleece or sweatshirt materials might scorch at higher heat, so adjust accordingly.
-
Other Fabrics (Nylon, Spandex, etc.): These aren't as common for DTF, but it's possible to apply to them with the right approach. Nylon is tricky – it often has coatings and low melt points. If attempting nylon, use low temp (around 275°F) and a longer press (maybe 15-20 seconds), and expect that not all DTF adhesives will stick to nylon well (some specialized adhesive may be needed). Spandex/Lycra (like athletic wear) can melt or warp with high heat; keep temperature under 290°F and keep press time brief (~8-10s). Also, stretchy fabrics may cause the print to crack if the garment is significantly stretched later; DTF on very stretchy fabric isn't generally recommended for heavy-duty use. Always test on a scrap or inconspicuous area for these unusual materials. For heat-sensitive fabrics, there are "low temp" DTF adhesive powders available that bond at around 250°F – using those with a lower press temp can save a delicate fabric from damage. Learn more about DTF printing on difficult substrates for specialized techniques.
Pro Tip: No matter the fabric, it's often helpful to pre-press the garment for 2-3 seconds before placing the transfer. This removes moisture and wrinkles, creating a flat, dry surface for better adhesion. After pre-pressing, let the garment cool a bit (especially important for poly) so you're not applying the transfer to a super-hot shirt which could trigger premature sticking or ghosting. Small steps like this contribute to a more reliable press.
Hot Peel vs. Cold Peel DTF Transfers
Another factor that affects your pressing workflow is the peel type of the DTF film. DTF transfer sheets are generally categorized as either hot peel or cold peel, referring to whether you remove the PET film carrier while it's still hot or only after it has cooled. The choice of hot vs. cold peel has implications for how you press and the finished result:
-
Hot Peel DTF Film: Hot peel transfers can be peeled off immediately (within a few seconds) after lifting the press, while the print is still hot. The film's release layer is formulated to let go of the ink when warm. Workflow impact: Hot peel is great for speed – you don't have to wait for the print to cool, which is a big advantage in batch production. You can press a shirt, open the press, peel the carrier off right away, and even immediately do a second press or move on to the next garment. This rapid application is why many commercial printers prefer hot peel for volume jobs like team uniforms or event merchandise. In terms of press settings, hot peel films often require slightly higher temperature or longer time than cold peel to ensure the adhesive fully releases from the film. For example, one source suggests ~330–375°F for 15 seconds for hot peel, versus ~320–350°F for 10–15 seconds for cold peel. Always check the specific instructions for your film. Results: Hot peel typically yields a glossy finish on the print – colors can appear very vibrant with a bit of sheen. The initial adhesion of hot peel is very strong, which is good, but interestingly it can lead to prints that are a touch less flexible. Some experts note that in long-term wash tests, hot peel prints have a slightly higher tendency to crack or deteriorate compared to cold peel prints. This is partly because peeling hot can sometimes force the ink to set more rigidly. Additionally, there can be minor color tone differences; hot peel transfers might not match exactly the colors of an equivalent cold peel (they can be a half-step off in hue or brightness). This usually isn't noticeable unless you compare side by side, but if color fidelity is critical (for example, a corporate logo color), keep this in mind. Overall, hot peel is favored for efficiency – it "gets the job done" fast and generally looks great, with the trade-off of a glossier look and marginally lower long-term durability.
-
Cold Peel DTF Film: Cold peel transfers require you to let the print cool down completely before removing the carrier film. The transfer should feel room temperature or only slightly warm – this usually means waiting 20-30 seconds at least, or you can speed it up by fanning the garment or placing it on a cool surface. Workflow impact: The need to wait adds a step/time to each item. In a one-off scenario this is no problem, but in production you'll either set the shirt aside to cool and start another, or if you have multiple platens (like a shuttle press) you can rotate. Cold peel is a bit slower; however, some shops manage it efficiently by doing all pressing first and peeling later after shirts have cooled in a pile. In terms of pressing, cold peel films tend to require slightly lower heat or a bit less pressure than hot peel, as their release layer works differently. Typical cold peel setting might be ~320°F for 12 seconds (where a comparable hot peel might be 330°F for 15s). Follow the manufacturer's spec – using too high heat on a cold peel film can actually make it harder to peel (the film may stick too much if overcooked). Results: Cold peel prints often have a matte or low-gloss finish, which many people like for a softer look. Because you peel after cooling, the adhesive has time to set with the fabric, usually resulting in a very strong bond. In fact, cold peel DTF transfers often outperform hot peel in durability – they tend to withstand more wash cycles with less cracking or fading. The prints can feel slightly softer/flex more, because the release process is gentler (the film isn't yanked off while everything is molten). Color-wise, cold peel is known for excellent fidelity and consistency. The main downside is just the slower pace of application. If you're doing many shirts, the waiting time can bottleneck you unless you organize a cooling station or use multiple presses. But for small runs or when maximum quality is desired, cold peel is very forgiving. There's less risk of messing up a print since you're not handling it hot – peeling cold means the design either comes off clean or if it doesn't, you can repress without having partially lifted it.
In summary, neither hot nor cold peel is "better" in all cases – it depends on your needs. If speed and efficiency are priority (e.g. large orders, on-site printing at events), hot peel is a winner, allowing quick turnover. If ultimate print quality, longevity, or a matte look is the goal, cold peel might be preferable. Some companies even offer a hybrid "warm peel" or universal film that can peel at warm or cold temperatures. No matter which you use, make sure to peel with a smooth, even motion. For hot peel, usually a swift, confident peel at 45° works best (don't hesitate or peel too slowly, as that can cause bits of ink to lift). For cold peel, peeling slowly is fine since the adhesive is set – just watch for any bits that didn't stick and press again if needed. Always refer to the instructions specific to the transfer film you purchase, as the chemistry can vary slightly across brands.
Troubleshooting Common DTF Heat Press Problems
Even with the right equipment and settings, you may encounter some issues when pressing DTF transfers. Here are some common problems and practical tips to troubleshoot them, as detailed in our comprehensive troubleshooting guide:
-
Uneven Pressure or Incomplete Transfer: If you notice parts of the design are not transferring or only sticking on one side, uneven pressure is a likely culprit. First, check that your platen is level and that the pressure is set firmly enough to reach all areas of the print. Thick seams, zippers, or buttons on a garment can prevent the press from closing flat, causing weak pressure on the design. The solution is to use a heat press pillow or pressing pad inside or under the area being printed to even out the thickness differences. For example, place a pillow in a shirt to raise the printing area above the seams – this helps distribute pressure uniformly. Also ensure you're using the correct size platen for the item; a design near a shirt collar might press unevenly on a too-large platen with the collar off to the side. If your press has an adjustable pressure knob, increase it slightly and re-press the transfer. Many times, simply pressing again with more pressure (and maybe +10°F extra heat) will fix a partially lifted design. On clamshell presses, remember that the back hinge can sometimes cause the front to have a bit less pressure – you might need to position the garment such that the thickest portion is toward the back, or just apply strong pressure. Inconsistent pressure between multiple presses is also something to watch: if one shirt comes out fine and another has issues, verify that nothing (like a twisted garment or debris on the platen) is skewing the pressure on the second try. Regular maintenance of your press (tightening any loose hinge bolts, etc.) will also help keep pressure even. A quick test is to place four strips of paper at the corners of the platen, close the press, and see if they all have equal drag when pulled – if one slips out too easily, you have a pressure unevenness to address.
-
Scorching or Fabric Discoloration: Scorch marks appear as an unwanted change of color on the fabric in the shape of the heat platen, often a yellowing on light colors or a darkening/shiny effect on darker fabrics. This is most common with high-poly content materials and some delicate cottons. If your garment is getting scorched (burnt) or a heat press box mark, the first thing to try is reducing the press temperature. For instance, if you were at 325°F and see scorching on a tri-blend shirt, drop to 315°F and see if the result improves. You can also shorten the press time and compensate by pressing twice (e.g. two 5-second presses instead of one 10-second press) to reduce the peak heat exposure. Pressure can contribute to scorching as well – very high pressure can physically imprint the fabric and cause a sheen. Interestingly, one recommended step if you see scorching is to reduce the pressure first before lowering temperature. Try using medium pressure instead of high, and use a protective cover sheet. Placing a piece of parchment paper or a silicone platen cover over the garment can help prevent direct contact and lessen scorch risk. Some heat press manufacturers sell non-stick covers for the upper platen that create a slight barrier and buffer the heat, which is helpful for sensitive fabrics (these also prevent the metal platen from touching the garment, thus avoiding shine marks). Also, be mindful of the garment's material: as discussed, polyesters can scorch at relatively low temps – so ensure you're within a safe range for that material. If you absolutely must press a sensitive fabric at a higher temp (perhaps for a certain transfer), inserting a thin cotton press cloth between the platen and garment can sometimes absorb a bit of heat. However, this may require increasing time or temperature slightly to compensate, so use that method carefully. In summary, scorching is solved by lowering heat, decreasing pressure, adding barriers, or all of the above. Once you dial in settings that apply the transfer without leaving a mark, stick to those for that fabric. (Note: a mild "heat press square" imprint often will disappear after the shirt cools for a few minutes or after the first wash, especially on cotton. If it's just a temporary flattening of fibers, that's not true scorching and is usually nothing to worry about.)
-
Poor Film Adhesion (Transfer Lifting or Peeling): This refers to when the DTF print doesn't fully stick to the garment – you go to peel the carrier and some or all of the ink stays on the film, or the design looks like it could be easily peeled off the shirt. The most common causes are insufficient heat or pressure, or peeling the carrier at the wrong temperature. To troubleshoot, the immediate fix is often: lay the carrier back down and press again. Increase your pressure if it was light, and add a few more seconds. You can also bump the temperature by ~10-15°F for the re-press. DTF transfers are fairly forgiving to multiple presses (the inks generally won't get ruined by an extra press or two). When you repress, use a parchment or Teflon sheet on top just in case any exposed adhesive might stick to the upper platen. Re-pressing usually fixes spots that didn't stick. However, you should also identify the root cause: Was the press not hot enough? (Double-check with a thermometer – maybe the machine reads 320°F but is actually cooler). Was the pressure too low? (After adjusting, note the new setting for next time). Did you perhaps peel a cold-peel transfer while it was still hot? (That would definitely cause poor adhesion – always wait until cool for cold-peel films). Moisture in the shirt can also steam and prevent a good bond, which is why pre-pressing is useful. Another issue could be incompatible fabric – e.g., trying to press onto a hydrophobic or coated fabric might yield bad adhesion. DTF works best on cotton, poly, and blends; something like nylon jacket material might not hold the adhesive well without special pretreatment. Assuming you're using a normal garment, nearly all poor-adhesion cases come down to refining the three settings discussed earlier. As a last resort, if one particular transfer just won't stick, you might have a bad transfer (low-quality film or powder). Using high-quality DTF transfer film/powder helps avoid problems. But in the moment, remember that you can always repress – DTF can be pressed multiple times until it's right, unlike sublimation or screen prints that you get only one chance. If you see an edge lifting after peeling, simply cover and press again for a few seconds; problem solved.
-
Cracking or Stiff Prints: If a DTF print cracks, it usually shows up after cooling or (more often) after one or more washes. A "stiff" print refers to a transfer that feels overly thick or crunchy on the garment. These issues can be related and often come from improper curing or pressing parameters. One cause of cracking is over-curing or over-pressing – too much heat can essentially bake the ink/powder to the point of brittleness. Ensure that you cured the film (if you printed it yourself) at the right temp/time, and that you're not pressing significantly longer or hotter than necessary. Cracking can also happen if the adhesive didn't fully melt into the fabric (then the design is more on the surface and can crack when flexed) – this could be due to not enough heat. So both extremes (too much or too little heat) might lead to cracks. The best prevention is using the correct press settings as discussed and doing a final finishing press after peeling the carrier. A second press of about 10-15 seconds with a cover sheet on top of the print can dramatically improve the durability and hand of a DTF print. This final press (sometimes called a post-press or "T-seal") melts the design into the fabric more and removes any residual moisture, making it less likely to crack and also softening the feel. It also often matte-ifies the print, reducing shine. So if your prints feel stiff or plasticky, definitely try a finishing press with a parchment paper on top – you'll notice they come out more flexible. Additionally, wash and care conditions play a big role in cracking over time. Always wash DTF-decorated garments inside-out on cold, gentle cycles to maximize life. High heat in a dryer can age prints faster. Educate your customers on proper care. If you're consistently seeing cracking, evaluate the materials: lower-quality DTF powders or films might not have the same elasticity as premium ones, leading to cracks. Also consider the fabric stretch: putting a non-stretchy transfer on a very stretchy fabric will cause cracks if the fabric is stretched (e.g., across the chest of a spandex workout top). In summary, most cracking/stiffness issues are mitigated by proper pressing and care: use the right temperature (avoid super high heat that overcures), ensure good adhesion, consider a final press for softness, and advise gentle washing. For specialty finishes that require different handling, consult specialized guides.
-
Fabric Shrinkage or Warping: Occasionally, you might observe that a garment has shrunk or become misshapen after pressing. This can manifest as the fabric looking "scalloped" or a transfer looking distorted. The primary cause is heat shrinkage of the fabric. Natural fibers like cotton can shrink a little when heated, and synthetics like polyester can actually shrink or melt if overheated. If you press a blank garment at too high a temperature, you may even see the outline of the platen as an area that's slightly smaller (shrunken) than the surrounding fabric. To avoid this, use the lowest effective temperature for the fabric type (as given in the guidelines above). For example, don't press a polyester item at 375°F just because your transfer can theoretically handle it – you'll cook the poor polyester. Another tip: performing a short pre-press can also pre-shrink the area under the heat a bit, so that when you do the actual transfer it doesn't shrink further. If warping occurs after peeling, it could be due to peeling a hot transfer off a still-flexible fabric – sometimes pulling the film stretches the garment slightly. Cold peeling avoids that since everything is cooled and stable. Fabric warping can also refer to the print area looking wrinkled after pressing; this can happen if the fabric had some give (like ribbed cotton) that got flattened. A gentle stretch while warm and then smoothing can reset the shape in some cases. If a garment did shrink noticeably (cotton can shrink a percent or two with heat), unfortunately that's permanent. Make sure you're not massively exceeding the recommended time – e.g., pressing for 60 seconds what should be 15 seconds – as that will definitely cause unnecessary shrink and possibly scorch. Lastly, certain heat press accessories can help: for instance, using a lower heat press temperature with a longer dwell might prevent sudden shrinkage. Some professionals use a technique of gradually heating: press 5 seconds, lift, press again 5 seconds, etc., to gently bring the fabric up to temp. This is rarely needed, but an interesting approach for extremely sensitive materials. In general, accurate temperature control is your best defense: ensure your press is truly at, say, 300°F when it says it is, and stick to proven settings for each fabric to prevent any unwanted fabric distortion. According to Wikipedia's article on heat pressing and industry standards from ASTM International, proper temperature control is crucial for preventing fabric damage during the transfer process.
By systematically addressing issues like these, you can quickly troubleshoot and refine your process. DTF is a relatively forgiving technology – most mistakes can be fixed with an extra press or adjusting a setting on the fly. Keep notes of what went wrong and how you solved it, so next time you can avoid the issue altogether.
Pro Tips for Consistent Results and Batch Production
Finally, let's cover some pro tips to help you achieve consistent, repeatable quality across multiple garments, especially in a batch production setting. These pointers will streamline your workflow and reduce errors:
-
Calibrate and Warm Up Your Heat Press: Consistency starts with your equipment. Always let your heat press fully warm up to the target temperature and stabilize before you start pressing shirts. An uncalibrated press can have cold spots that lead to inconsistent results. Use a laser IR thermometer or heat test strips on different areas of the platen to ensure even heating (at least occasionally, or when you suspect an issue). If you find your press runs hot or cold compared to the readout, adjust your settings accordingly. Also, during long production runs, the lower platen may heat up or the upper platen temperature can fluctuate when pressing continuously. Some presses have an indicator when they drop a few degrees. It's good practice to pause for a moment if needed to let the press climb back to proper temp every so often. This ensures the first shirt and the 50th shirt receive the same heat and pressure. According to the National Institute of Standards and Technology (NIST) and equipment manufacturers like Epson and Roland, accurate temperature measurement is essential for quality control in manufacturing processes.
-
Use Pre-Press and Consistent Placement: Develop a routine for each garment. For example, a typical process: position the shirt on the platen (using guides or a ruler for alignment if needed), pre-press 2 seconds (to flatten and remove moisture), position the transfer (using tape if necessary to hold it), press for the required time, peel, then do a final press. Doing this sequence the same way each time builds consistency. Especially in batch jobs, using a placement guide or laser alignment tool can be helpful so every design is positioned uniformly on each garment. Something as simple as a T-square ruler or a template for left-chest logos will save time and keep your output looking professional.
-
Optimize Your Workspace for Batch Production: If you're pressing dozens or hundreds of items, organize your work area for efficiency. Keep the transfers within reach (and in order if they are personalized). Have a "hot pile" and "cool pile" system – for cold peel jobs, you might press a shirt then move it to a cooling table and grab a cooled one to peel. This way the press is never sitting idle waiting on a peel. For hot peel, you can have a heat-resistant glove to peel immediately and toss the finished shirt aside. The idea is to minimize the downtime between presses. Auto-open presses are excellent for preventing over-pressing and letting you multitask (you won't scorch a shirt by forgetting it in the press, and you can be prepping the next garment while one is pressing). If your press doesn't auto-open, use that timer and stay attentive. Some users attach a loud buzzer or use a phone timer as a backup. In batch production, every second counts, but consistency and avoiding mistakes is even more important – so find a rhythm that is fast but controlled. Learn more about scaling your DTF production business for advanced strategies.
-
Keep Your Press Clean and Maintained: A well-maintained press produces consistent results. Over time, adhesive residue or ink might build up on the platen or cover sheet. Clean it off (when cool) because those residues can affect heat conduction and even ruin garments if they stick or stain. For example, a little melted adhesive on the upper platen can leave a random glue spot on the next shirt – not good. Use a scraper or rag to remove gunk, or Teflon platen covers which can be easily wiped. Check the pressure mechanism and hinges periodically – lubricate if recommended by the manufacturer – so that the press closes uniformly. For pneumatic units, drain the compressor moisture trap and maintain proper air pressure. Consistency in maintenance will reflect in consistency in pressing. Also, protect your platens: use parchment or Teflon sheets when appropriate to avoid direct contact with the transfer, especially if any adhesive might squeeze out. It's easier to replace a sheet than to clean a platen mid-run.
-
Leverage Tools for Even Pressure: When doing a batch of varied items (say a mix of T-shirts and hoodies, or items with seams), be prepared to adjust. Have a set of heat-resistant foam pads or different platen sizes to swap out. For example, sliding a pad inside a hoodie ensures the thick seams don't reduce pressure on the design area – giving you consistent results whether it's a tee or a thick hoodie. If you press a lot of thick garments, consider a press with a pressure gauge so you can note the PSI for each product (e.g., 60 PSI for tees, 80 PSI for hoodies) and quickly dial it in when you switch. This removes guesswork and keeps prints looking uniform. Even on manual presses, you can mark or remember turns of the pressure knob for different items. The use of heat press pillows, as mentioned, is a quick fix for many pressure issues – they "fill" the gaps under zippers or buttons and maintain even pressure.
-
Standardize Your Settings and Test When in Doubt: Once you find the ideal temperature, time, and pressure for a certain transfer and garment combination, stick to it. Create a chart or checklist that your team can follow. For instance: "For our supplier's hot-peel transfers on 100% cotton tees: 330°F, 12 sec, firm pressure, hot peel, then 5-sec final press." Having these standard settings documented ensures that if multiple operators or shifts are involved, they all use the same parameters, yielding consistent output. When you receive a new batch of transfers (especially from a different supplier), don't assume they press exactly the same – do a test print on a scrap fabric to verify the settings. A few minutes of testing can save you from ruining a batch. If you're pressing large numbers, test at the start of each day or whenever you suspect something is off (e.g., humidity is high that day, or you moved the press). It's also a good idea to do wash tests for a new transfer type: press a sample, run it through a laundry cycle, and see if it holds up. This helps catch any issues with adhesion or curing before you commit to selling the product. Quality control standards as outlined by our quality assurance checklist are essential for consistent results.
-
Workflow Hacks for High Volumes: In a production environment, little tricks can boost efficiency while keeping quality high. For example, lay out the next garment while the current one is pressing (just be mindful of safety – clear the area before the press opens if it's an auto-open clamshell to avoid it hitting anything). If you have access to a dual-platen (shuttle) press, use its capacity to the fullest: always be loading one side while the other side is pressing. Keep an eye on the cycle times to get into a steady rhythm. Another tip: group your jobs by type – press all the cotton tees that use the same settings in one batch, then adjust settings and do all the polys, etc. This minimizes changing temperatures and setup. Consistency in batches is easier to maintain than constantly switching back and forth. Also, maintain consistent room conditions if possible; extreme cold in a workshop, for example, can cool your platens faster or make transfers stiff. A climate-controlled environment isn't always feasible, but avoid direct drafts or cold airflow on the press area if you can (it can cause uneven heating). For more insights on production efficiency, check out our guide on advanced DTF automation and workflow optimization.
-
Keep Safety in Mind: Consistency also means consistently safe practices – a burnt or damaged garment (or worse, an injured operator) will interrupt your batch real fast. Use heat-resistant gloves or finger cots when peeling hot transfers to protect yourself and also to allow a confident peel. If multiple people are working, have clear communication, e.g., call out "pressing" or "opening" if needed. Ensure you have adequate ventilation especially when doing large batches, as the process can release some fumes from the melting adhesive. A small fan or open window (not blowing directly on the press) can help. And of course, never leave the press on unattended – modern presses have auto-shutoff timers; use them, especially in busy production where it's easy to get distracted at break time. The Occupational Safety and Health Administration (OSHA) provides guidelines for workplace safety when working with heat-generating equipment. Additional safety resources are available through SGS and Testex certification services.
By incorporating these pro tips, you can create an efficient production workflow where each DTF print is as good as the last. Remember that consistency is about both the technical settings and the human process. With well-calibrated equipment from trusted manufacturers like Brother, Mimaki, and Mutoh, standardized settings, a tidy workflow, and attention to detail, your DTF transfers will come out looking crisp and lasting long on every garment, whether you're making one custom shirt or a run of five hundred.
Continue Your DTF Education
Perfect your heat pressing techniques with more advanced guides at Iris Academy:
- DTF Color Management: Advanced Artwork & ICC Profiles
- Mastering DTF Adhesive Powder: Complete Application & Curing Guide
- DTF Printer Maintenance: Essential Troubleshooting Guide
- Specialty Inks & Finishes: Advanced DTF Techniques
- Common DTF Pitfalls: Ultimate Troubleshooting Solutions
Stay informed about the latest heat pressing innovations through professional publications like Impressions Magazine, Printwear Magazine, and connect with industry experts at FESPA events. Quality consumables from suppliers like Stahls', Siser, and Chemica can enhance your heat pressing results.